Festo Introduces New Generation of Electric Actuators for Linear Applications
Festo’s new actuators are designed to improve axis performance while enabling high loads in a compact footprint.
May 7, 2024
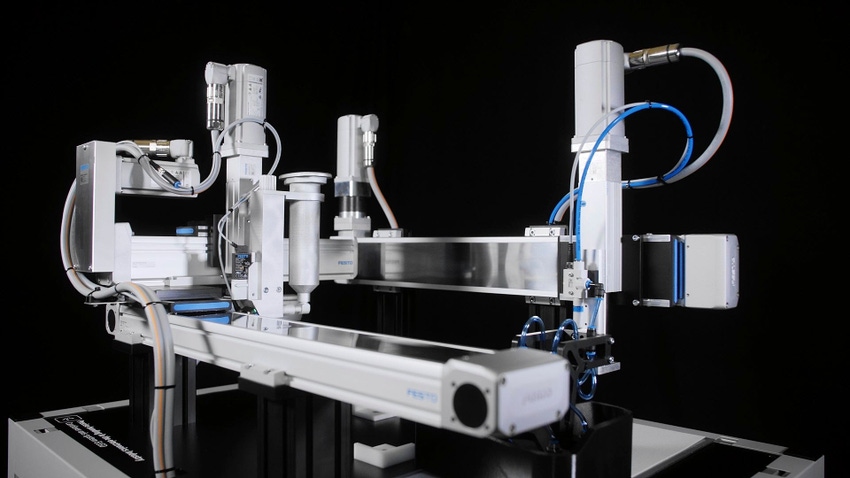
At a Glance
- This enhancement was designed to enable high loads in a compact footprint.
- The actuators are based on a new Festo design.
Festo has introduced its newest generation of Cartesian-handling-system mechanical axes. The ELGD-TB, tooth belt actuators, and ELGD-BS, ball screw actuators, are based on a new Festo design.
Festo noted that its start-to-finish management of every aspect of the ELGD series design, testing, and manufacture ensures world-class quality, a robust and reliable supply chain for assured availability, and industry leading price/performance. ELGD axes deliver exceptional load bearing capacity and torsional rigidity, long service life, and increased reliability in multiple industrial handling situations, from dirty to cleanroom environments.
Suited to most electromechanical handling tasks, the ELGD series brings specific benefits to applications, such as:
Cantilever systems and pick-and-place solutions for small parts handling, where short cycle times, high precision, and repeatability are key
Handling systems for top loaders, which benefit from the ELGD’s attractive price/performance ratio, high travel speed, and long stroke lengths
Automation of 3D printing, additive manufacturing, dosing, gluing, and picking and placing are enhanced with the ELGD’s dynamic, virtually vibration-free movement.
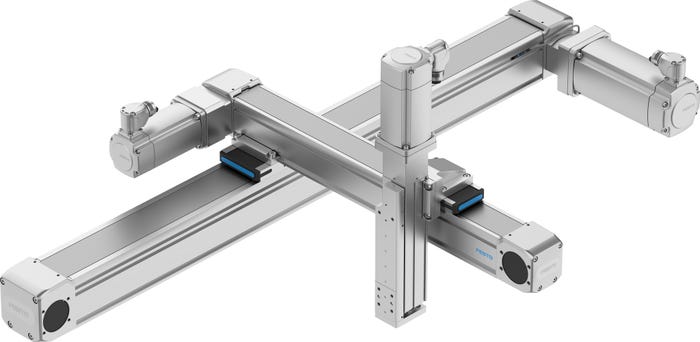
Image courtesy of Festo
Smaller, More Powerful Axis
Festo inlaid the bearings into the aluminum extrusion and extended bearings to the full width of the axis. This design enhancement enables high loads in a compact footprint. Machine builders can pack even more powerful tooth belt or ball screw axes in smaller footprint systems to achieve excellent feed forces and acceleration profiles. The integrated bearing design also enabled Festo to develop the lower profile ELGD-WD (wide actuator) for reduced force applications. This low-profile ELGD is 30% lighter than larger units while its rigidity and guide load capacity are similar.
With the Festo Electric Motion Sizing online productivity tool, design engineers input application parameters and the tool finds the right combination of CMMT multi-protocol servo drive, Festo servo or stepper motor, and accessories for the axis with all components perfectly sized and interoperable.
In 2025, the ELGD axis series will be integrated into the Festo Handling Guide Online (HGO) tool for multi-axis handling system sizing and selection. HGO enables users to design a complete cartesian solution in under 20 minutes, including CAD models and documentation. The Handling System arrives as a kit and is fast and easy to assemble with Festo mounting brackets. ELGD axes are also compatible with third-party motors. Festo offers a range of mounting hardware to make third-party motor mounting a snap.
The ELGD-BS ball screw drive offers configurable stroke lengths up to 8.2 ft. The ELGD-TB toothed belt drive provides stroke lengths of up to 27.9 ft. The ELGD series gives a choice of carriage options, including a long carriage and additional passive carriage. The long carriage integrates a second pair of split ball bearing cartridges, which provides even greater permissible torques to the carriage for the most dynamic applications. The passive second carriage allows the loads on the guidance to be distributed even further, essentially doubling the maximum permissible torques, load capacity, and service life for the mechanics in the application.
The ELGD features a stainless-steel cover strip, which minimizes particle emissions in cleanroom applications and reduces ingress of particles in dirty environments. Festo enhanced particle emissions capability by including a pneumatic connection to provide sealing air (0.1 – 0.2 Bar) or a vacuum to the internal structure of the mechanics. Another innovation is the magnetic deflection of the cover strip, which eliminates mechanical wear and further reduces the likelihood of particle emissions.
Read more about:
Supplier NewsAbout the Author(s)
You May Also Like