Designing Safety: The Critical Role of Cleanliness in Aerospace Oxygen Systems
Precision cleaning must be engineered into the product development plan before production begins.
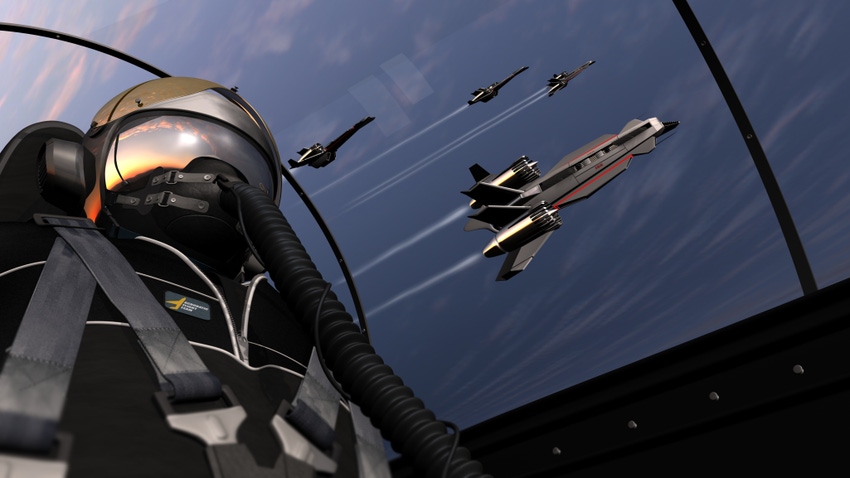
At a Glance
- Contaminants present possible risks of combustion, auto-ignition, or explosions within oxygen-rich systems.
- Potential solutions include mechanical cleaning, aqueous cleaning, and vapor degreasing.
- One method stands out, given its suitability for precision cleaning.
For the aerospace engineers and manufacturers responsible for designing and producing aircraft oxygen systems, ensuring absolute cleanliness is quite literally a life-or-death imperative. Even microscopic contaminants left behind on internal part surfaces from manufacturing processes can pose catastrophic combustion hazards that jeopardize the entire aircraft and the lives of those aboard.
The grave consequences of contamination in these critical life support systems underscore why achieving the meticulous cleanliness and safety demands requires far more than just robust cleaning at the end of the manufacturing process. Instead, it requires making cleanliness a fundamental design driver by engineering precision cleaning into the product plan from the very outset before production even begins.
Contaminant Hazards Demand Cleaning
Aircraft oxygen systems consist of complex networks of tubing, valves, regulators, sensors, and other components that distribute oxygen from cryogenic liquid or chemical sources to masks, outlets, and portable breathing equipment. Typical contaminants introduced during manufacturing include dust, welding dross, metal particulate debris, and hydrocarbon-based greases and oils, as well as inorganic pollutants like water-based cutting oils and solvents. Although these contaminants may not be visible to the naked eye, it is critical that every single part is precision cleaned to remove all contamination for system performance and safety.
If any production contamination stays on the parts, it has the potential to generate possible combustion, auto-ignition, or even explosions within oxygen-rich systems. Moreover, as the flammable ranges expand and the auto-ignition temperatures of materials used in oxygen systems decrease, they become increasingly susceptible to ignition. Any remaining particulate can spontaneously ignite in these delicate atmospheres. Therefore, every system part must undergo thorough cleaning and drying.
While fire safety is still the primary motivation for cleaning oxygen system components, other factors must also be considered. Particles or residues left behind during the manufacturing process have the potential to disrupt the functionality of sensors, valves, and controls. Furthermore, components integral to the safe operation of oxygen systems must adhere to stringent industry quality standards. Failure to sufficiently clean and dry these components will result in their failure to meet the strict inspection and regulatory requirements.
Cleanliness From the Design Stages
To reliably produce perfectly clean and safe oxygen components and assemblies every time, cleanliness must be a focal point from the earliest design phases—not an afterthought once manufacturing is underway.
During the product development stage, thorough assessments should be conducted to find any areas where contaminants could accumulate based on the geometries of the parts. With high-risk areas pinpointed, designs can be adjusted to enhance 'cleanability' and meet effective cleanliness requirements. This includes defining maximum acceptable contaminant levels, cleaning chemistries, process parameters, and test procedures for verifying cleanliness.
By prioritizing cleaning throughout the design process, manufacturers can mitigate contamination risks, enhance product quality, and ensure compliance with rigorous industry standards before oxygen system production, assembly, and installation.
![Vapor_Degreaser_Overview[91].jpg Vapor_Degreaser_Overview[91].jpg](https://eu-images.contentstack.com/v3/assets/blt0bbd1b20253587c0/bltabb81904d7acb837/663a99cc9dbe5c50f601982d/Vapor_Degreaser_Overview[91].jpg?width=700&auto=webp&quality=80&disable=upscale)
The process of vapor degreasing. MICROCARE
Cleaning Methods
There are different methods for cleaning components used in aerospace oxygen systems. One method, mechanical cleaning, involves the use of a wire brush, sandblasting, or grinding to cut scale, paint, coatings, or welding dross. While this approach can be effective to a certain extent, it may also result in the generation of particulate residue.
Aqueous cleaning is another popular method. This process, whether with or without detergents and spray agitation, typically uses hot water or steam to remove water-soluble contaminants. This process, however, has drawbacks, including the need to rinse off detergent and dry parts before further processing. It also consumes significant water and energy, requiring multiple washing, rinsing, and drying cycles. Furthermore, it generates a wastewater stream that needs treatment before disposal.
Alternatively, vapor degreasing offers an effective cleaning method for aerospace oxygen systems. Utilizing advanced cleaning fluids, vapor degreasing efficiently removes contamination from parts, even penetrating blind holes and tiny openings inaccessible to aqueous cleaning. This ensures thorough cleaning and drying of all part surfaces, meeting precise standards for further processing or packaging.
Vapor degreasing is particularly suited for precision cleaning. The low viscosity and low volatility of modern non-flammable cleaning fluids allow them to flow effectively into tight spaces, evaporating quickly without leaving residue or posing a significant flammability risk. Furthermore, vapor degreasing aligns with rigorous industry regulations, such as ASTM G93 - 03(2011), the ‘Standard Practice for Cleaning Methods and Cleanliness Levels for Material and Equipment Used in Oxygen-Enriched Environments.’ This ensures compliance with cleanliness standards for oxygen-enriched environments.
Advanced vapor degreasing fluids also address environmental concerns. They are formulated with low-VOC compositions that are ozone-friendly and compliant with various regulations, including those set by the United States EPA and European directives. Unlike aqueous cleaning, vapor degreasing removes pyrogens, ensuring a bacteria-free environment for oxygen systems.
Compatible with a range of materials, vapor degreasing is safe for delicate parts like gaskets and seals due to its low boiling point and heat of vaporization. Additionally, this cleaning method offers a simple and repeatable process, helping ease qualification and validation, which is essential for meeting quality standards in oxygen system manufacturing.
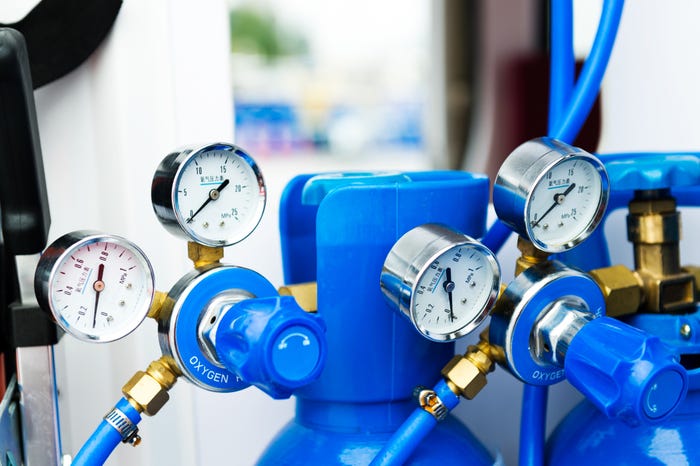
Oxygen systems consist of complex networks of tubing, valves, regulators, sensors. BAONA/ISTOCK/GETTY IMAGES PLUS VIA GETTY IMAGES
Cleared for Operations
For aerospace manufacturers, ensuring absolute cleanliness in aircraft oxygen systems is vital for protecting lives at high altitudes. By making cleanliness a core design priority and implementing advanced cleaning methods like vapor degreasing, manufacturers can reliably produce components that meet strict safety standards. Close collaboration between design engineers, producers, and cleaning fluid providers is key to consistently achieving the precision cleanliness required in these critical systems. As oxygen systems evolve, refining cleaning processes will remain essential for safeguarding the highest levels of cleanliness and safety in flight.
About the Author(s)
You May Also Like