Hip simulator helps control bone loss
August 14, 1995
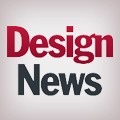
Watertown, MA--Perhaps a third of some 300,000 hip replacements performed in the U.S. each year are undermined because of a condition called periprosthetic osteolysis. It develops when the body's immune system tries to destroy small foreign particles ground off the prosthetic joint by normal wear of its polyethylene acetabular cup. The cup holds the prosthesis' cobalt-chrome steel ball. Bone erosion at the ball caused by the body's immune system damages the joint, making further surgery necessary.
Dr. William Harris, chief of orthopedic surgery at the Massachusetts General Hospital in Boston, asked Advanced Mechanical Technology Inc., (AMTI), to design and build a machine that accurately simulates the conditions encountered by a prosthesis in a human body. (AMTI is a spinoff from the Massachusetts Institute of Technology, where Walter Syniuta, the company's president, taught courses on friction and wear.) Harris also designs prostheses, and he believed the machine could help designers to better understand wear, and adjust the design of a prosthesis to minimize wear.
The machine Dr. Harris wanted would be able to simulate the motions, loads and temperatures experienced by a prosthesis as a patient walks or runs. Proper simulation requires enclosing the joint in a fluid that simulates the body's joint lubricant--called synovial fluid--with its blood and protein components.
Working with Dr. Harris and his colleagues at the Orthopedic Biomechanics Laboratory at Massachusetts General, AMTI developed a single-station machine in early 1992, and tested it for five million cycles. Satisfied with the results, Dr. Harris asked AMTI to step up to 12 stations.
Called the AMTI-Boston hip simulator, the machine has 12 identical stations arranged in two rows of six. Each station comes equipped with load cells that enable the system to continuously acquire force and motion data in three axes. Two thermocouples at each station monitor temperatures. There are 96 analog outputs from the stations (72 loads and 24 temperatures) gathered by a data-acquisition system. Heating elements under the machine's top plate hold temperatures in each prosthesis at about 37C.
"System kinematics closely match those of the human gait cycle," Syniuta says. "The acetabular cup is mounted in an upright position, and is subjected to n28 degrees of flexion and as much as n10 degrees of abduction--the swing of the hip joint outward to the side of the body."
Within each of the dozen prostheses under test, the unit's femoral head applies a joint reaction force through a post attached to a hydraulic cylinder. All 12 cylinders share a common manifold, ensuring that each cylinder experiences the same inlet pressure and load.
The load cells accommodate loads as great as 1,000 lbs, and provide six outputs--three each of force and moment (Fx, Fy, Fz, Mx, My, Mz). They employ a precision cylindrical element to isolate and measure applied forces and moments, strain gages, and high-gain amplifiers to boost signals.
Data from the load cells are acquired by a 486-based host computer. In turn, the computer relies on an 80-MHz 80C166 microcontroller to provide continuous waveform signals that control the system's mechanical actuators. An operator can program any desired waveform into the system, including a Paul-type curve, which simulates the motions the hip joint experiences when a user takes a step.
Cerebral palsy gait analysis
Sports medicine
Biomechanical Space Shuttle research
Each station has a chamber that protects articulating components. The chamber is sealed with a sterile saline IV bag. Every chamber includes one inlet and one outlet port to circulate lubricant, bathing the components of the prosthesis. The lubricant, bovine serum, "closely approximates the blood and protein of human synovial fluid," Syniuta says. This fluid circulates through an external reservoir, which can either heat or cool the lubricant to keep the bath temperature in a range from 25 to 50C.
Among other things, the simulator's electronics can plot the weight lost by the polyethylene prosthesis materials, allowing designers to measure the degree of wear.
AMTI is modifying the hip simulator's electronics, and is building nine more simulators. These units include two more hip simulators for Massachusetts General and three knee simulators for other customers.
Additional details...Contact Walter Syniuta, Advanced Mechanical Technology, Inc., 176 Waltham St., Watertown, MA 02172, (617) 926-6700.
About the Author(s)
You May Also Like