Sensor technology's changing skyline
July 16, 2001
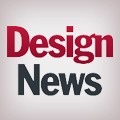
Optimized triple coils extend sensor range
In the Q80 embeddable proximity sensor, Turck has taken its patented Uprox(R) technology and, according to Robb Black, sensor division director, optimized the system's two sensing coils to extend the range of detection of all metals out to 50 mm (up from 40 mm for previous embeddable sensors) for automotive, materials handling, and conveyor applications. A third (oscillator) coil in the sensor induces an eddy current in the target, which then produces a vector difference between the equal voltages in twin air-core detecting coils (see diagram). Because sensing only depends on the vector difference in voltages, there is no temperature limit on the sensor beyond that of sensor materials, he adds.
When no target is present to the Uprox sensor, voltages E1 and E2 are not equal or in phase. Oscillator current is thus low and the device is at a non-resonant frequency of 680 kHz. As a target approaches, mutual inductance from eddy currents in the target's metal surface shifts the frequency up to 700 kHz and E1 + E2 = 0, allowing current to flow, giving a sensor output. The target passes by the sensor, but E1 and E2 remain equal and 180 degrees out of phase with each other, vectorally adding to zero. By using this vector-differences method, the sensing range is independent of the material present. |
Unlike conventional proximity sensors with a single oscillator coil, there is no ferrite core within the coil to obtain the needed high resonant quality factor (Q). Instead Turck designers use three precisely wound (tailoring the number of turns and wire size) and positioned coils. Without a ferrite core, Black says the sensors do not become saturated in high magnetic fields, such as near welding equipment on automotive production lines. And without having to oscillate a magnetic field in a ferrite core, sensor speed is "up to ten times that of a standard sensor," Black adds.
In addition to the long range, Black notes engineers were able to economize with a one-piece plastic potted housing. The sensor can be embedded within a floor or side structure of a machine, shielding it from damage-causing impacts. Options include the company's eurofast(R) quick connector for standard 12-mm connections.
For more information, Turck, www.turck.com; or Enter 549
DeviceNet comes to wide-ranging ultrasonic sensors
Hyde Park Electronics designers now have DeviceNet communications capability in their Ultrasonic SUPERPROX(R) SM956 30 mm Sensor Series. Mark Wagner, manufacturing test engineer, says surface mount technology electronics and new, smaller microprocessors were vital in putting this functionality into a compact package.
The Hyde Park Electronics DeviceNet capable SM956 30-mm diameter sensors come in stainless steel (left) or plastic housings and meet NEMA 4X and IP67 standards. Epoxy encapsulation resists shock, vibration, and harsh conditions. |
DeviceNet decreases downtime, with fast, device-level diagnostics, and reduces installation cost. The 30-mm diameter units are 60% smaller than other sensors with the same functionality and are aimed at applications in loop control, monitoring material levels in bins and bowls, and controlling distance. The sensors can range out to do detection at 1 or 2m. The 1-m model, Wagner adds, "has a short deadband that allows measuring to inside of 2 inches." Dual-crystal technology, with separate transmitter and receiver crystals, is responsible for this close-range capability, he notes, because the receiver does not have to damp down before it is able to detect a return signal.
Unlike light-based sensing, ultrasonic sensors are minimally affected by dirt and dust, splashing fluids, caustic solutions, humidity, and high-pressure wash downs.
For more information, Hyde Park Electronics, www.hpsensors.com; or Enter 550
'High beam' light barrier
Severe levels of contamination, such as dust found in the lumber industry, make position sensing with light barriers difficult, if not impossible. The EA250/SA250 series of light receivers and transmitters from Wenglor Sensors operate with a high-intensity infrared light beam so strong it can peer through ten sheets of standard white paper. For ease of mounting and to keep the size of the receiver and transmitter units as small as possible, they are linked to a common control unit.
The LV250 Control Unit controls up to three receiver and transmitter pairs. But using the control unit's cascade facility, nine control units can be operated together to give a light barrier system consisting of up to 27 receiver/transmitter pairs. One control unit is designated as the master that monitors the other units as slaves. Jurgen Sprenger of Wenglor's electronics development section points out, "We've tried to simplify the setup as far as possible. Cascading does not involve any addressing and there are no miniature dual in-line switches that need to be set." A single strip connector interconnects the nine control units.
An automatic teach-in feature, furthermore, proves useful in applications where the sensor configuration changes frequently. Because each light-barrier pair has its own output on the control unit, switching status of the individual barriers can be interrogated. A group output, reflecting the logical state of the sensors connected to the control unit, supplies a signal monitoring all of the light barriers simultaneously. A simple selector switch in conjunction with a row of LEDs on top of the control is used for setup, mode selection, and indication.
For more information, www.wenglor-sensors.com ; or Enter 551
Collimated LED gives laserlike position sensor performance
With a starting price of $279, the Banner Engineering L-GAGETM Q50 Light-Gauging Analog Output Sensor gives laser position-sensor performance at one-third or less cost than that of a laser-based sensor, according to Technical Marketing Manager Mike Dean. He notes the key to achieving this precision is the exacting spherical lens bonded to the LED light source, resulting in a highly collimated beam of infrared or visible light, depending on the LED used. Another lens focuses this beam into a 1.5-cm (0.6-inch) diameter spot for use in tight spaces or on small targets. An image of the spot on the target passes through another lens into a detector to determine target position (see figure).
A precise, spherical lens bonded to an LED emitter produces a highly collimated beam in Banner Engineering's Q50 triangulation sensor. Image of hte resulting spot on a diffuse-surface target passes through a focusing lens onto an analog photodiode receiving element. The ration of output current from each end of the detector (I1/I2) provides target position determination. |
The Q50's microprocessor eliminates the need for a separate controller, easing set-up time using a built-in teach mode. With a visible red LED, sensing range is 4 to 12 inches and with an infrared emitter range is 4 to 16 inches because of the detector's greater sensitivity at this wavelength. The user can select an output response speed of 4 or 64 msec. The sensor is designed for use in applications including dry-bulk level measurement, package filling, and loop control.
Dean adds that, as with a laser sensor, highly mirrorlike targets that would reflect the light spot in only one direction, are not suitable for detection with the sensor. While ultrasonic sensors could be used for position detection, the target must be very nearly perpendicular and in a "benign" environment.
For more information, Banner Engineering, www.bannerengineering.com; or Enter 552
Laser sensor reliably reads invisible markings
The SMARTEYE(R)STEALTH sensor from Tri-Tronics permits positive detection of invisible markings. Because it is red laser-based, the near infrared fluorescence induced in a specially formulated ClirCode(R) marking material from Isotag Technologies occurs in a portion of the electromagnetic spectrum away from natural fluorescence wavelengths activated by ultraviolet (UV) light-mitigating false readings. And unlike UV lamps, the laser-diode light source is immune to failure due to vibration. Sensor response time is 200 microseconds with leading edge variation less than 40 microseconds.
Dennis Henderson, vice president and sales manager, notes the sensor is aimed at security applications and those manufacturers who do not want registration marks or codes visible on their products. The chemical technology for the ink was developed by Los Alamos National Laboratory and the oil industry for security marking uses, Henderson notes.
The ClirCode can be formulated into water- or solvent-based materials such as inks, plastics, or adhesives and applied directly on materials. Any background is suitable, Henderson says, "except dark blue and black which absorb the red light." The sensor comes in three models: a long range (up to 8 inches) device for detecting large objects and marks; a convergent one with maximum sensitivity at 3 inches for small marking detection; and a model with a fiber optic light guide for sensing when a site is spacewise difficult to access or has a harsh temperature, vibration, or corrosion environment.
For more information, Tri-Tronics, www.ttco.com; or Enter 553
Accurate angle measurement at low cost
Sensors based on optical principles are often used to measure the angle of rotation on shafts. But such sensors are too expensive and bulky for many applications. One alternative, now offered by Novotechnik Stiftung & Co., is a non-contact Hall-effect angle sensor. Developed in conjunction with the Technical University (ETH) at Lausanne, Switzerland, the VX22 angle sensor consists of a cross-shaped piece of silicon in which each of the two limbs (x and y) form a vertical Hall sensor.
Like a normal Hall sensor, a voltage is produced across a current-carrying conductor when subjected to a magnetic field. The conductor, though, is split and folded back on itself with the electrodes on one side. In this configuration, the magnetic field flows parallel to the limbs of the cross in the x-y plane producing, as the angle varies, a voltage proportional to the sine of the rotated angle on one limb, and a voltage proportional to the cosine on the other limb. The two voltages are digitized and evaluated using a microprocessor, giving a 12-bit resolution. Depending on the application, the output may be digital or analog.
Josef Albano, product manager for the VX22, quotes an accuracy on the measured position of 0.35 degrees. He also adds, "Hysteresis on the angle measurement comes in at a barely measurable 0.045 degrees." Since the only part subject to wear is the ball bearing for the shaft, he expects a sensor service life of at least 100,000 hours. In principle, any of the commonly used interfaces can be realized digitally and a CAN bus interface is planned. Due to the low friction drive, a typical application for the new sensor is on remotely indicating wind-vanes.
For more information, Novotechnik Stiftung, www.novotechnik.com; or Enter 554
About the Author(s)
You May Also Like