Sensor ensures drug labeling
June 4, 2001
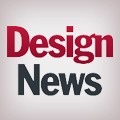
San Antonio -DPT Laboratories, an outsourcing company for drugs and cosmetics, wanted to improve its production process in confirming that bottles delivered from its plant had the proper front and back labels. DPT was relying on line workers to visually check each bottle for labels before packing it into a case. To automate and error proof the process, a team headed by DPT electrical engineer Les Casler began evaluating various vision systems and sensors.
The group first found a vision system that not only detected whether each bottle had a label, but could measure the label's area, locate its center, and determine the height of the bottle. But it also had a complex set of tools not required for the label-presence application. Another downside was tens of thousands of dollars in initial cost plus significant training and maintenance.
Casler's team also looked at a low-contrast fiber-optic sensor from Banner Engineering (Minneapolis, MN). With this system, a separate photoelectric sensor served as a "gate" sensor, sending a signal to the machine's PLC when it detected the leading edge of each bottle. The PLC then triggered the fiber optic sensor to determine whether it was receiving light reflected from a label or from a bottle (label missing).
While the initial cost of this system was much lower and its operation much simpler, the designers still had versatility issues. If each machine could be used for only one type of bottle and label, the fiber optic system would have been feasible. However, DPT Laboratories packages more than 400 types of bottles with various shapes, sizes, colors, and materials. And, the labels themselves have many variations. Thus, with each line change, technicians would need to reposition the sensors to read each new bottle size and shape. They would also have to recalibrate the sensor amplifiers. Some bottle-and-label combinations required another sensor amplifier altogether to emit a different color beam (green, blue, red, or white). Such time-consuming complications ate into the system's cost advantages.
Previously, a separate gate sensor detected a bottle, triggering a fiber optic sensor to look for a label. This system's sensors needed repositioning for each change of product on the line. |
Third time a charm. Last year, Casler's group evaluated Banner's new PresencePLUS(TM) pixel-counting sensor. Like the fiber-optic system, a photoelectric gate sensor senses the leading edge of bottles, triggering inspection. But unlike the single-point fiber optic sensor, the PresencePLUS scans an area measuring 1.3 x 1.0 inches, thus obviating line changes to reposition the sensor.
The PresencePLUS sensor is able to capture a 512- x 384-pixel grayscale image of the bottles being processed. Processing algorithms then convert the grayscale image to black or white pixels, depending on a user-adjusted threshold. The system then counts the pixels to render a pass/fail decision.
DPT Laboratories now uses more than 20 PresencePLUS sensors on lines running three eight-hour shifts per day. And up to four times each shift, line workers will change over to another label and bottle combination. Part of their line-change routine is to run several bottles with and without labels to teach the PresencePLUS which bottles to pass or fail. The technicians use a push-button "teaching pendant" to program the sensors.
The teaching pendant may be removed and given only to authorized technicians, but it is not necessary for sensor operation. The resulting absence of buttons or potentiometers on the sensor body prevents line workers from inadvertently taking the sensor out of calibration and causing down time. However, because of DPT Laboratories' frequent product changes and the abundance of technicians, the teaching pendants remain connected to their sensors. A security code allows only authorized technicians to teach the sensor new run-time parameters. When the line is running, the pendants are configured to continually display a "run/judge" screen which shows current condensed images and numeric pixel counts with the running pass or fail percentage.
DPT engineers are now evaluating PresencePLUS sensors for additional applications such as inspecting bottles for the presence of date-code printing.
For more information about sensors and vision systems from Banner Engineering: Enter 540
About the Author(s)
You May Also Like