Prototypes Speed Festo's Endurance Testing
October 11, 2007
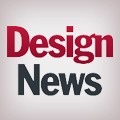
For an idea of just how far additive manufacturing technologies have come–and how far they have to go–consider the experience of Festo. This supplier of advanced pneumatic and electric automation systems, recently revealed some of its successes and struggles with additive fabrication during an International Media Day held Germany.
Festo’s in-house additive production capabilities center on Stratasys fused deposition modeling systems, which have produced more than 30,000 plastic prototypes of pneumatic components over the past 14 years, reports Klaus Müller-Lohmeier, a Festo technology manager.
In recent years, the company has increasingly turned to various metal-based additive processes, including direct metal laser sintering from EOS, selective laser melting from MCP Systems, and the LaserCUSING laser sintering system from Concept Laser.
Festo has yet to make any production metal parts on additive systems, but its functional prototypes come pretty darn close. As Müller-Lohmeier explains, Festo subjects all its new products to high-cycle mechanical tests, and it uses additive machines to build test specimens. To hold up to the endurances tests, the additive parts must be dense against air pressures as high as 16 bar and capable of withstanding tens of millions of load cycles.
The endurance test parts also have be produced in materials comparable to the ones it uses for its production parts. Running steel on an additive machine is a no-brainer. But Festo makes extensive use of die-cast aluminum and has only recently been able to find suppliers capable of running aluminum alloys on laser-based additive machines.
Festo has already used additive technologies to help develop a variety of products, including MPA1 valve terminals and VSVA Series valves. In his lab, Müller-Lohmeier even shows off a complete pneumatic circuit, consisting of about 50 parts made on additive machines. “It contains no serial production at all,” he says.
In the past, Festo’s endurance tests created a time-consuming bottleneck in its product development process. Engineers could sometimes spend months waiting for the die-cast tooling or metal-injection molds needed to produce truly functional prototypes. Müller-Lohmeier says these “time gaps in the development cycle,” could last from a few weeks for machined parts to up to seven months for some metal-injection-molded components.
With additive machines, Festo can get functional parts in hours or days and start endurance tests much earlier in its product development cycle. “We can eliminate design flaws early, when the cost of change is the least expensive,” says Müller-Lohmeier, who estimates that additive fabrication technologies have shaved 25 percent off Festo’s typical product development time.
Now that Festo has started to produce functional prototypes that can hold up to long-term tests, is direct digital manufacturing of production parts just around the corner? Well, not quite. Müller-Lohmeier argues that metal parts produced on additive machines do have some subtle differences from cast or molded parts made from the same nominal material. The density of the additive aluminum parts, for example, tends to exceed that of cast parts by about 1 percent, according to Müller-Lohmeier. The tensile properties of the additive parts are also slightly higher.
Density and tensile properties improvements are normally an advantage, but they also mean that the additive parts could perform differently–not necessarily worse–than familiar die cast parts. “The long-term behavior of the prototypes is not known,” says Müller-Lohmeier. The most important unknowns he cites are fatigue life, wear properties and media resistance.
Take economics into account and the near-term case against direct digital manufacturing is even more clear cut. Given current technologies and Festo’s production volumes, additive parts simply cost too much to be viable, according to Müller-Lohmeier. He even displays one aluminum part that cost more than $5,500 dollars. “We don’t do any destructive testing on this one,” he jokes. And he says that the average cost of the metal functional prototypes exceeds $1,400 based on a machine-hour rate of roughly $64 per hour.
Manufacturing on additive machines may become viable in the future as engineering companies such as Festo develop more confidence in the long-term material properties and as the additive machines themselves become more productive. “Direct manufacturing is not yet suitable for Festo,” Müller-Lohmeier says, “But there is hope that it will be within the next ten years.”
About the Author(s)
You May Also Like