Design for Manufacturability (DFM) for Early-Stage Companies
Here’s how to address mechanical challenges as you transition from proof-of-concept design to a full-production design.
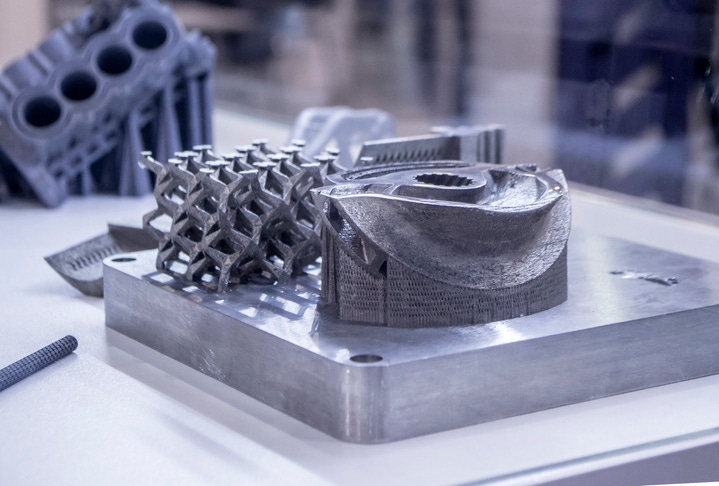
Early-stage companies face difficult trade-off challenges when transitioning from design and build of one to two units to larger-scale production. At high volumes (i.e., 10,000+ units), the Design for Manufacturability (DFM) challenges and solutions are well known and understood. However, there is a gap. How do designers deal with the challenge of going from a build of less than 10 units to 500 or 1000 units? This presents a unique set of challenges because early-stage companies rarely have the capital necessary to move directly from a proof-of-concept design to a full-production design.
Such teams need to create product designs with ultimate production in mind. And, it is important to get quotations on production quantities in various processes, as this is helpful in cost analysis of when to transition to volume-production manufacturing techniques.
One approach for prototyping is the use of rapid prototyping parts. While they can be made from machined raw materials, more common these days is the use of inexpensive, fused deposition method (FDM) printed parts. In addition to the use of FDM systems, there is a more-recent class of multi-jet fusion (MJF) machines capable of simultaneously producing more parts at a higher rate of speed with improved mechanical properties. And stereolithography (SLA) systems are still in use particularly in applications requiring fine resolution. The nice thing about these processes is that there are a wide variety of materials available that can get very close to production-quality material properties.
For metal parts, there are rapid prototyping options using sintered metal: direct metal laser sintering (DMLS), sintered laser melting (SLM), or selective laser sintering (SLS) systems. The technology for rapid prototyping continues to evolve with seemingly new materials and processes being released every year.
For higher-volume plastic-part prototypes, silicone mold processes are still in common use. A silicone mold can typically yield 50-100 parts. It can be hard to simulate the mechanical properties and details of an injection-molded part using this process, but it is an option for many situations, particularly where durability is not critical. The molds are inexpensive, but the production rate can be fairly slow.
Moving up from this, the next step is aluminum injection mold tooling, which is as close as you can get to production-quality injection molding without investment in hardened steel tools. Since aluminum can be machined more easily than tool steel, the molds can be created more quickly than for tool steel. There are some limitations on use of an aluminum tool when it comes to sophisticated use of slides and other actions. The more complex the needs in the tool, the less likely that aluminum is the right choice (at least not without sacrificing tool life). Aluminum tools can be good for 2000-10,000 pieces.
Of course, for some plastic parts, extrusions and vacuum forming may be appropriate. The tooling cost for these is low, making them appropriate for even moderate-volume prototypes. Of course, there are limitations with the feature definition in formed tools and obvious restrictions as to shape when one is using extruded shapes.
It is important to remember that there may be limitations on the aesthetics or features accuracy of rapid prototyped parts. Going in with anything other than soft aluminum tooled parts may mean that secondary operations may be required. Such operations can improve aesthetics and features precision, with the downside of needing to add another layer of cost.
The key is to have a plan on what production volumes are needed to be addressed in the interim period (prior to high volume). Then, select the right process to produce parts based on the appropriate quality and production costs for the specific volume required.
Companies large and small all have to consider DFM in the design process. Early-stage companies often have a difficult challenge balancing good processes and design optimization with the practical realities of capital constraints. These companies should go into product development with a plan for how they will take a design from early concept stages through low-volume production with a mind toward ultimate high-volume manufacture.
About the Author(s)
You May Also Like