New powder press is petite but powerful
July 10, 2001
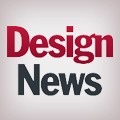
Friday, December 1, 2000
West Lebanon, NH--Size does matter at Mii Technologies. This maker of powder metal components and materials has created a diminutive hydraulic press that packs more than twice the clamping force of conventional powder metal machinery into a fraction of the space.
Make that a tiny fraction. While a 220-ton powder metal press typically stands at least 20 feet high and has the girth of a garbage truck, the new 458-ton Mii press takes up less room than a kitchen refrigerator. "We traded brute force for a better design," says Glenn Beane, Mii's president and the machine's principle designer.
More than just an effort in downsizing, the press represents just one part of an modular approach to powder metal manufacturing. In contrast to the usual collection of stand-alone presses, Mii's manufacturing system uses a centralized hydraulic "power plant" to drive a plant of small, powerful presses. Individual machines tap into the central plant via a 450 psi feeder line--a procedure Beane likens to "plugging in an extension cord." And with the bulk of the hydraulics removed from the press, only a relatively small clamping mechanism remains.
Mii's manufacturing cells--or "docking stations," as Beane calls them--also employ unique material-handling capabilities to boost the uniformity that sometimes eludes metal powder processes. For part-to-part uniformity, Mii's cells have a gravimetric feeding system controlling the amount of powder that enters the die. "It's accurate to within one-tenth of a gram," Beane notes. And to achieve a uniform density within a part, Mii developed a patented vacuum system to fluidize the powdered metal in the die, evenly distributing it.
The system compacts material differently than a traditional press, too. As Beane explains, traditional presses drive the punches in lockstep without regard for localized resistance in the die--which result from part geometry or uneven powder distribution. He says this condition can strain individual punches, ruining parts at best and breaking tooling at worst. Mii's system backs each punch with a hydraulic piston. Each one operates individually with closed loop control of pressure, distance, and time.
A PC-based controller runs the entire system--everything from the material handling systems to the punch-piston controls.
Taken together, Mii's innovations cut the cost of making complex, high-volume powder metal parts by 30-50%, Beane claims. "We can produce parts that traditional powder metal processing can't make cost effectively," he says. In fact, a fuel injection solenoid actuator that stymied traditional powder metal processes drove Mii to develop its new press concept back in 1997. Since then, Mii has used the system to produce precision components using its own soft magnetic materials and steels. Just last month, the company made the system available for license.
For more information, visit www.miitechnologies.com.
About the Author(s)
You May Also Like