New Packaging Plastic Is Made From Carbon Dioxide
December 15, 2009
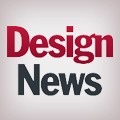
Several consumer products companies are testing a new plastic made half from carbon dioxide and half from hydrocarbon feedstocks in equipment formerly used by Kodak to make chemicals and film for its photographic business.
Novomer, a startup company based in Ithaca, NY, will use its proprietary zinc-based catalysts to produce a plastic called aliphatic polypropylene carbonate, which is said to provide an excellent oxygen barrier, as well as good impact and other mechanical properties. Mike Slowik, manager of strategic planning and analysis for Novomer, says: “In some cases, the properties can be better than traditional petroleum-based plastics.” One example, he says, is an Improved oxygen barrier. “The material could also be used for lighweighting because it has great impact resistance and stiffness,” says Slowik.
Target applications include soda bottles, containers and food wrap. Competing materials are polypropylene, polystyrene and polyvinyl chloride. On a mass production basis, Novomer hopes its PPC can be cost competitive with those materials, which typically cost 75 cents to 99 cents per pound. Right now, however, quantities are only being made in batches of 10 to 30 pounds at a time.
Initially, consumer products companies were given small amounts of the polymer from Novomer’s R&D lab in Ithaca. “They have been able to independently verify some of our results and they want larger quantities so that they can injection mold it,” says Slowik. “They want to see it how it performs on some of their conversion equipment.”
The quality of Novomer’s environmental argument has been debated on some Web sites.
Early in its development, Novomer officials said they hoped to use citrus fruits as feedstocks. Slowik told Design News that use of citrus fruits is still under evaluation. Novomer obviously feels the route under development at Kodak will produce better economics. Kodak is functioning as a contract manufacturer on the project.
The environmental argument is that half of the feedstocks are carbon dioxides. Initially the gas will come in containers from distributors. Long-term, it could come from scrubbers on power plants or cement factories. The other feedstock is propylene oxide, a derivative of oil production.
Novomer’s early plans also called for development of a biodegradable polymer. The PPC is not degradable, which Slowik says is good because it sequesters the carbon dioxide.
There is no question the Novomer news is a welcome development in Rochester, NY, which has been severely affected by the downturn in the photographic film business. No estimates are available on the amount of film-making capacity that has been idled at Kodak’s facilities but no doubt it is substantial.
The commercialization project is funded by an $800,000 grant from the New York State Energy Research and Development Authority. Also partnering in the project is the Rochester Institute of Technology, which is performing tests on the new film material.
The magic in the Novomer technology is a catalyst developed by Cornell professor Geoffrey Coates that creates long-chain molecules from carbon monoxide and carbon dioxide at room temperature. One advantage of the Novomer technology is that it’s all based on synthetic chemistry, unlike biopolymers that use bacteria.
Novomer is also developing aliphatic polyethylene carbonate (PEC) and polyhydroxyalkanoate (PHA). The PEC is made from ethylene oxide instead of propylene oxide. One PEC grade has already been commercialized and is being used in electronics manufacturing.
The photo shows tests on Novomer’s new polymer being extruded at Kodak facilities in Rochester, NY.
About the Author(s)
You May Also Like