Invertebrates Inspire 3D-Printed Flexible Robotic Actuators
Researchers have 3D-printed flexible and active robotic actuators to create robots with a wider range of motion.
May 4, 2018
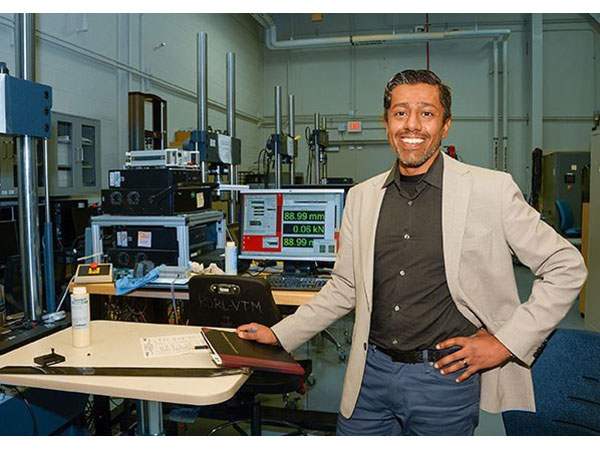
A joint project between the University of Minnesota and the U.S. Army Research Laboratory (ARL) studied invertebrates—animals that possess neither skeleton nor bone—to solve a problem with the robotic systems that the Army currently employs.
Typically, Army robots are structurally rigid, which limits how the military can use them—especially in congested urban areas in situations where they need to perform covert military operations, said Dr. Ed Habtour, an ARL researcher specializing in nonlinear structural dynamics, who worked on the project.
Dr. Ed Habtour works in the US Army Research Laboratory's Vehicle Technology Directorate, where he specializes in nonlinear dynamical systems. He was part of a team that used inspiration from invertebrates to develop a process to 3D-print flexible robotic actuators. (Image source: Conrad Johnson, US Army) |
Current military robots have two key limitations restricting them from performing the maneuvers required, he said. First, they lack the necessary dynamic flexibility, as they mainly comprise rigid mechanical and electronic components. Secondly, these rigid robots require complex mechanical infrastructure and electrical circuitries to achieve active actuation and complex modes of motion, according to Habtour.
"Successful stealthy maneuvering requires high structural flexibility and distributive control to sneak into confined or restricted spaces, operate for extended periods, and emulate biological morphologies and adaptability," he said.
To solve these issues, Habtour and his collaborative team developed soft actuator prototypes using active materials with parameters—such as structural flexibility, morphology, and dynamic actuation—that they can fine-tune. Researchers said that their work demonstrates an example of the first fully 3D-printed dielectric elastomer actuator (DEA), which can perform high-bending motions.
READ MORE ARTICLES ON 3D PRINTING:
By studying invertebrates, the team was able to identify ways to achieve more flexible ways for robots to move, researchers said. From these observations, they took a two-step approach to their work, with the university providing the former and the ARL providing the latter.
First, the team used a custom 3D printing platform to build and test a prototype similar to the actuators they observed in nature. To this end, the university 3D-printed distributed actuation circuitries. These involved soft, stretchable materials with mechanical properties similar to biological organisms, such as cephalopods and worms, researchers said.
Then, the team developed a unified mathematical model to study the sensitivity of each parameter they identified for novel ways to make the robot move, predicting the various optimal actuation mechanisms.
This was the task of Army researchers, who identified two key mechanisms for enabling high-bending motion in soft biological actuators, Habtour said. The first was to tune physical properties by exploiting the interplay between the materials and dynamic nonlinearities to augment the motion. The second was to highlight the electromechanical coupling between the electrical field and nonlinear structural stiffness through the distributive actuation circuitries.
The researchers’ findings provide a key step toward giving the solider “an autonomous freeform fabrication platform”—that is, a next-generation 3D printer that can fabricate functional materials and devices—“to generate soft actuators and potentially tetherless soft robots on demand, on the fly, and at the point of need," Habtour said.
Researchers published a paper on their research in the journal Extreme Mechanics Letters.
Elizabeth Montalbano is a freelance writer who has written about technology and culture for 20 years. She has lived and worked as a professional journalist in Phoenix, San Francisco, and New York City. In her free time, she enjoys surfing, traveling, music, yoga, and cooking. She currently resides in a village on the southwest coast of Portugal.
About the Author(s)
You May Also Like