Engineering News 7388
April 10, 1995
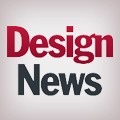
Lasers expand the machine-tool envelope
Newton, MA-Lasers may never supplant drilling, milling, and grinding for the mass of industrial production, but make no mistake-they're changing the definition of what machine tools do.
Higher-performance assemblies
Lower-cost tooling
Greater design flexibility
Advances in laser machining technology include higher power, higher precision beams, a shift to fiber-optic-transmissible wavelengths, and the promise of machined micromachines.
Although laser machine tools still represent a small portion of the entire machine tool market, their share is increasing, according to Charles Carter, vice president of the Association for Manufacturing Technology. "It reflects their growth in cost effectiveness in delivering power to a workpiece, as well as their flexibility in precision cutting and welding of thin materials," he says.
Industry sources say that these advances will mean more options for designers, including:
Easier integration of composite materials
Smaller heat-affected zones around holes and joints
More-rigid structures through continuous, one-sided welds as opposed to spot-welded construction
Lower-cost cutting of sheet-metal shapes without creation of punches and dies
Laser machining progress can be seen in the rapid development of neodymium: yttrium aluminum garnet (Nd:YAG) lasers. Compared to more widely used CO2 lasers, these solid-state devices are more easily cooled and offer more robust design. In addition, their shorter wavelength can be transmitted through fiber-optic cables instead of the precision waveguides needed for longer-wavelength sources.
At 3,000W, the HLP 3000 from Hobart Lasers & Ad-vanced Systems, Troy, OH, claims to be the most powerful continuous-wave Nd:YAG laser available. "That power translates into greater cutting and welding speed-up to 180 inches per minute," explains company President Harrison Hobart. The lamp-pumped system delivers its 1.06-aem beam through a 600-aem-core-diameter fiber-optic cable up to 150m long, and permits multiplexing of a single laser generator among several machining workstations.
Because it's not pulsed, the laser permits continuous weld lines between parts during assembly operations. Moreover, those welds can be performed from a single side of the assembly. These two features, coupled with the multi-axis flexibility of robotic laser welders, will permit automobile designers to eliminate many of the frame holes now necessary for access to resistance spot welders and create better welds at the same time, says Hobart. The result: higher fatigue life and stiffer car bodies.
Solid-state lasers. The promise of completely solid-state Nd:YAG lasers prompted the federal government to enter into a technology-reinvestment project with a consortium of 16 companies to accelerate the laser's development. Pumped by diodes, not flashlamps, such systems offer improved reliability and even higher speeds.
According to Len Marabella, program manager for consortium-leader TRW, Inc., Redondo Beach, CA, the Precision Laser Machining project focuses on developing two new capabilities. One, a 2.5-kW average, 25-MW peak-power pulsed laser, will cut and drill metals and composites more quickly and accurately than currently possible. The second, a 6-kW average long-pulse model, will specialize in welding and heat-treating applications.
With beta-site testing expected in 1996, Marabella reports progress has been rapid. The new machines should offer clear advantages to designers, he says.
"Greater speed and accuracy reduces the heat-affected zone around the laser-processing site, improving the material performance of the finished product."
The flexibility of robotic equipment fitted with fiber-optic-delivered lasers should reduce fixturing costs, making more-frequent design im-provements an economic possibility. And, since the laser source never touches the part surface, there's no worry about the cost of broken tools and concomitant downtime.
Micromachining laser. Another laser technology originally developed for defense purposes now seeking commercial applications: the visible-light copper laser. Richard Foster-Turner of Oxford Lasers, Inc., Acton, MA, explained the copper laser's advantages at the recent National Design Engineering Show. "Its green wavelength couples well with metals and silicon as opposed to IR lasers, where metals are highly reflective and silicon, transparent."
Pulsing at 30 to 40 nsec, the copper laser's 50W average translates into 200-kW peak power. "The material-removal event is over quickly," says Foster-Turner. "It can drill high-aspect ratio holes 1.5-aem in diameter with negligible heat-affected zones." The visible wavelength beam also simplifies operations. Machinists use an attenuated beam for alignment with the workpiece, then step up the power for processing.
Applications include drilling holes for fine-mist ink jets, creating through-vias in ceramic-substrate circuit boards, scribing photovoltaic cells, crack-simulation, and machining natural and polycrystalline diamonds. In the future, the company envisions manufacturing micromachines directly without environmentally questionable chemical processes.
For the moment, Oxford's main business is in materials evaluation and contract manufacturing. Why exhibit at a design show? "This represents a new capability," says Foster-Turner. "The shows always have people with drawings and new ideas for it."
SGI to merge with Alias, Wavefront
Mountain View, CA-Silicon Graphics Inc. will acquire Alias Research and Wavefront Technologies in a half-billion-dollar merger-a move analysts say may speed the development of design-software technology.
SGI, known primarily for its powerful graphics workstations, will form a software subsidiary to develop "the world's most advanced tools for the creation of digital content," the companies say.
"The tools still have a long way to go," Rob Burgess, Alias president and CEO and now president of the new subsidiary, told Design News. He envisions a new generation of tools that will allow industrial designers to work on computers as they now work with paper or foam - for example, picking up a marker and "sketching," instead of using a mouse or tablet. Such tools would also incorporate precise geometry, making it easier for engineers to preserve the intent of an industrial design.
"I think the amount of R&D going into their underlying technologies will steadily increase," says Bruce Jenkins, with the Cambridge, MA-based Daratech research firm. While the initial focus may be on the lucrative entertainment market, he expects the same technologies to be incorporated into engineering design tools as well. The entertainment industry has joined defense and aerospace as a place where important new technology is spawned, he notes.
Alias, based in Toronto, is a leading automotive and industrial-design software company, whose customers include BMW, Caterpillar, Ford, and Motorola. Wavefront develops graphic imaging and animation software. Both companies have a major presence in the television and moviemaking industries.
Grad students propel robots in new directions
Newton, MA-Hollywood gave us The Terminator and Robocop, but it's our nation's universities that give us the silicon-wafer ant and robotuna. Not as glamorous as their film counterparts, these research robots are providing more than entertainment, though-they're supplying a glimpse of the future of locomotion.
The fish. For example, at M.I.T in Cambridge, MA, students are looking to Mother Nature for a better mini-submarine design. Their project began more than three years ago with one goal in mind: develop a better propulsion system for autonomous underwater vehicles, or AUVs.
These robotic submarines can map the ocean floor or find underwater pollution sources. But, "you simply can't put enough batteries on-board for long-term missions like exploring the mid-Atlantic ridge for a couple of months," states ocean-engineering graduate student David Barrett.
Realizing the fish has 160 million years of evolution behind it, researchers used the bluefin tuna as a model. The result was Charlie the Testing Tank Tuna.
About four feet long, this "fish-bot" actually "swishes" its tail to propel itself down M.I.T.'s research tank. The current prototype is attached to a structure that houses all its electronics and guides it down the tank.
While the ultimate goal is a fully autonomous robot, researchers are focusing their efforts on getting the tunafish robot to swim efficiently in a straight line.
The CAT. Meanwhile, at Rensselaer Polytechnic Institute, graduate student Adam Divelbiss is more concerned with wheels than fins.
For his doctoral thesis, Divelbiss sought a mathematical solution to a class of problems where movement is constrained by velocity or acceleration. Parallel parking proved to be an excellent example, he says.
Working with associate professor John T. Wen, Divelbiss designed a quarter-size test vehicle. Called the CATmobile, after the Center for Advanced Technology (CAT), the vehicle pulls two trailers. Divelbiss then wrote a computer program that automatically maneuvers the vehicle into a tight parking space.
The student-professor team equipped the vehicle with sensors to measure steering and jackknife angles, and to predict vehicle position. The feedback system makes real-time corrections, and holds the vehicle to the desired path.
With a few adjustments, the computer system could be used as an on-board assistant to help truck drivers with difficult maneuvers or control a robotic convoy in an automated factory, says Wen.
And the ant. Within Room 717 of Boston University's Research Center, there is a robot being designed that anyone could overlook. Measuring only 3 aem thick, this silicon microrobot, when complete, would be capable of walking in a tripod gait.
The six-legged "ant," which is too small to use motors for leg actuation, moves via a piezo-electric actuator. Most recent developments in its design have been completed by Masters-degree graduate Jayanthy Goli.
So far, piezoelectric ZnO sandwiched between two gold layers for electrodes has been the tested actuator material of choice. Legs were then connected to the actuator, creating a tilting motion when an alternating voltage source is applied.
The micromachine, when complete, could be used in "poison gas detection, DNA sequencing, and even espionage," says Smits.
'World's first' dual-cyclone vacuum cleaner
Chippenham, England-Dyson Appliances Ltd., with a design assist from the Dutch chemical group DSM, has designed what it claims to be the world's first dual-cyclone vacuum cleaner. The design features a patented dual-cyclonic action that separates the dust or water from the incoming air. The advantage: no filter is needed, and the suction power remains at a constant, high level.
The innovative vacuum consists of three different polymers produced by DSM, Heerlen, The Netherlands: Ronfalin(R) ABS, Xantar(R) polycarbonate, and Stamylan P(R) polypropylene. DSM's technical specialists developed a three-dimensional model, then simulated the mold flow for more than 30 plastic parts that make up the appliance.
In addition, DSM formulated the special Fantasy Color that gives the vacuum's housing a metallic appearance. The Ronfalin grade selected combines a very high gloss with excellent flow properties. Xantar was chosen for the reservoir due to its transparency and impact resistance, while the Stamylan P polypropylene's price/performance ratio made it ideal for such components as the filter system.
"Sales in England have been going exceptionally well," says James Dyson, "with a drive now underway to cover the entire European marketplace."
Polymer-based transistor's breakthrough: It's flexible
Thiais, FRANCE-A polymer-based transistor developed here could play a significant role in a generation of products that need flexibility-such as computer and television screens that can roll up and down.
Researchers at the Centre National de Recherche Scientifique (CNRS) have created an organic semiconducting material whose characteristics resemble those of amorphous silicon. They used the material to construct a transistor on which the electrodes are composed of graphite-based polymer ink.
The screen printing methods used in producing the transistor-which is still in the prototype stage-are low cost since they do not require enormous amounts of energy, high temperatures, or vacuums the way silicon devices do. On the other hand, the disadvantage is that they do not have a high resolution so the size of the devices is likely to be many times larger than those currently made of silicon.
Because of its size, the all-polymer transistor will not replace existing silicon-based devices, but is likely to suit applications characterized by high flexibility, low cost, and a large area, says Francis Garnier, research scientist at the CNRS' molecular materials laboratory. It could, for example, be used in information displays on car and plane windscreens because the flexible polymer transistor could be easily applied to the curved form of the windscreen.
Garnier predicts that commercial applications for the all-polymer transistor will be developed in about five years.
Among the initial applications likely is the smart card, he says. Smart cards today are liable to break because the interface between the flexible plastic card and the rigid semiconductor device it incorporates is fragile. This could be solved if the device was also flexible, and the transistor could be the solution, Garnier says.
-Anna Kochan, European Editor, France
Software aids shovel design
Milwaukee-Engineers in the Mining Equipment Division of Harnischfeger Corp. turned to The Mac-Neal-Schwendler Corp.'s MSC/NASTRAN finite element analysis software to ensure the ruggedness of their new P&H 4100 electric shovel.
With a 55-cubic-yard dipper, the shovel digs and deposits 82.5-ton payloads in three passes to fully load a 240-ton truck.
"We used MSC/NASTRAN to predict stress levels and the behavior of components, then we evaluated the data against established historical profiles," says Bill Powers, staff engineer. Specific parts of the shovel analyzed: dipper body, twin-leg dipper handle, and deep mid-section boom.
Powers used the software's cyclic symmetry option. It allows engineers to save time by modeling only half of a symmetrical model and then get results for both sides.
Lab fashions fluid-control components
Yellow Springs, OH-In applications ranging from automobile engines to hospital catheters, Vernay Labs' flow-control devices must withstand a variety of demanding tasks while surviving high pressures, vacuums, and caustic or hot fluids-and still remain elastic and durable.
Using ANVIL-5000 software from Manufacturing and Consulting Services, Inc., Scottsdale, AZ, has made most design jobs 25 to 50% faster at Vernay Labs, estimates Tom Rex, design supervisor and tool engineer. One example: a production mold for making a needle valve with 144 cavities. Vernay's family of parts are similar enough, Rex says, that designers can take different upper and lower cavities and use them to generate a new mold structure.
The company uses its CAD models to download crucial design information for finite element anaylsis in popular formats such as IGES or DXF.
CAD helps design custom-fit workouts
Falmouth, KY-When Shaquille O'Neal wants customized exercise equipment, you don't want to keep him waiting. Hammer/Strength, Inc. understands this need, and uses a 3-D CAD system from Hewlett-Packard to save design time-and keep "The Shaq" and other customers happy.
Hammer/Strength, Inc., a Falmouth, KY-based customized exercise equipment supplier, uses the ME Series 30 to design, test, and analyze new exercise machines using "Reggie," a fully functional digital model.
"Reggie" is modeled on Reggie Williams, a former all-pro linebacker for the Cincinnati Bengals. Using two HP 9000 workstations, this 3-D solid model provides enough information on weight, balance, and movement so no physical model is needed.
The system's macro language also allows Hammer/Strength to change Reggie's size to accommodate women or smaller men, for example, since commonly used design features, such as geometric calculations or standard library parts, are completely automated. In addition, the company uses VDS Environment, customization macros provided by Visionary Design Systems, to boost productivity.
Gary Jones, founder, vice president, and director of manufacturing and engineering for Hammer/Strength, says HP ME CAD is easy to use. "What used to take days on paper or an hour on a traditional CAD system we can do in seconds," he says. "And we get a perfect fit and alignment."
To customize the machines, the process begins with Jones, seated in a dentist's chair with angle gauges, discussing exercise needs with the customer and a staff physiologist. Jones then returns to the workstation, places Reggie in his own chair on the screen, and moves him through natural human motions, digitizing the motion's axis of rotation. Those measurements build the arm of the proposed machine, the part of the machine that moves. Finally, a seat for Reggie is built in 3-D space based on those specs. The rest of the machine is then built around Reggie.
Future plans for Hammer/Strength Inc. include the possibility of developing ergonomically-correct equipment for the office. Says Jones: "If we can think it, we can do it."
Denver airport finally in the bag
Denver, CO-Eighteen miles northeast of Denver and 30 feet underground lie 2 miles of train track upon which 30 million people a year will entrust their travels.
Or at least their luggage.
The track belongs to Denver International Airport's (DIA) fully-automated baggage handling system which, by an order of magnitude, is the largest in the world.
Developed by BAE Automated Systems (Dallas, TX), it consists of a fleet of 3,100 standard-size and 450 oversize destination-coded vehicles (DCV), or Telecars. DCVs roll the rails unpowered on sealed-bearing urethane wheels and resemble fiberglass updates of old-time mining cars. Regular DCVs handle bags up to 120 lbs, while the 6.5- x 4-ft oversized cars manage 350-lbs of skis, bikes or golf clubs.
Twenty-one hundred linear induction motors mounted beneath the track propel the cars at up to 1,750 fpm. Merges and loading operations occur at a more leisurely 600 to 700 fpm under the control of a friction drive and brake system. Concerned with aerodynamics and the possibility of blowing bags out of a car, engineers analyzed the DCVs in a wind tunnel.
Radio transponders attached to each car provide tracking data to a set of 55 networked computers running a custom Windows-based control program. The data is gathered by 400 radio-frequency identification (RFID) readers spaced at 150 to 200-ft intervals. Using inductive coupling, the readers interrogate the unpowered transponders allowing the system to guide full cars, manage empty cars, and identify problems with the cars or the track.
A bag's journey begins at check-in when agents attach a bar-coded destination tag. It then descends to a queue on a portion of the system's six miles of conveyors, passing one of 56 laser scanners on the way. The scanner reads the tag and triggers the computer to summon an empty DCV.
Like California commuters, bags ride one to a car. The system knows which DCV picked up which bag, and it uses RFID, not the bar-code tag, to steer bags to the proper gate. At the gate, the bag is either deposited in a holding area or passed to a conveyor and fed directly to the aircraft's cargo hold.
BAE has been blamed in part for a nearly two-year delay in the airport's completion (service began Feb. 28). The tardiness stems, BAE says, not from widely reported software glitches, gross "empty car" management problems, and fundamental design errors, but from the normal-yet unexpectedly lengthy-teething problems of a system 10 times larger than any ever built. "We simply underestimated the time needed to fine-tune a system of this size," says Gene Di Fonso, BAE's president. "It was like going from a DC-3 to a 747 without intermediate steps."
Problems that did challenge BAE engineers involved accurate speed control at merge points, motor overloads, temperature variations, and inadequate control of empty cars. To improve speed control, designers added LIMs and braking magnets. To prevent overloads they installed harmonic line filters. And to solve temperature-induced belt stretch, the system is now warmed daily.
Although intended to serve all three terminals, only United Airlines-DIA's largest tenant-fully utilizes the baggage system. Others exploit small portions of it with the option to expand usage later.
DIA itself inspires description with superlatives-or obscenities. It covers the most land (53 square miles), supports the tallest control tower (327 feet), has some of the thickest runways, and at $4.9-billion dollars is the most expensive US public works project ever.
Oh, and of course it houses the most expensive ($230-mil) automated baggage handling system ever conceived. As it turns out, BAE's biggest mistake may not have been in engineering, but in public relations. Says Di Fonso: "The first time you push the button on anything, you're bringing yourself nothing but grief by doing it in front of an audience."
KEY SUPPLIERS
PRODUCT | SUPPLIER | LOCATION |
---|---|---|
LINEAR INDUCTION MOTORS | CALDWELL ELECTRIC | WACO, TX |
ROTARY INDUCTION MOTORS | BALDOR ELECTRIC | FT. SMITH, AR |
GEAR REDUCERS | MORSE | FLORENCE, KY |
CLUTCH BRAKES | WARNER ELECTRICS | BELOIT, IL |
TIMING BELTS | GATES RUBBER | DENVER, CO |
COMPUTERS | TEXAS MICROSYSTEMS | HOUSTON, TX |
PROGRAMMABLE CONTROLLERS | SQUARE D CO. | MILWAUKEE, WI |
ELECTRICAL CONTROLS | ALLEN BRADLEY CO. | MILWAUKEE, WI |
LASER BAR CODE SCANNERS | LAZER DATA CORP. | SANFORD, FL |
CONVEYOR BELTING | GEORGIA DUCK | SCOTTDALE, GA |
BEARINGS | MORSE SEALMASTER | FLORENCE, KY |
POWER TURN CONVEYORS | PORTEC | CANON CITY, CO |
EXTENDIBLE CONVEYORS | CALJAN AMERICA | DENVER, CO |
ELECTRICAL CABINETS | HOFFMAN ENGINEERING | ANOKA, MI |
RFID SUBSYSTEMS | INDALA | SAN JOSE, CA |
VERTICAL LIFTS | P FLOW INDUSTRIES | MILWAUKEE, WI |
WHEEL TREADS | AMERICAN URETHANE | GAMBRILLS, MD |
Spacehab test mission drives valve redesign
Huntsville, AL-Engineering a manufacturing process can be difficult enough. Try designing one where all the components operate well in zero gravity and meet NASA's strict manned-flight qualifications.
Dr. James E. Smith of the University of Alabama confronted this problem and met it. His job: Create a liquid-phase sintering process that could fly on NASA's first Spacehab mission on the shuttle Endeavor in 1993. And in the process, Smith compelled his suppliers to redesign their components to meet his unconventional needs.
In liquid-phase sintering, two or more metal powders are compacted into a billet and heated above the melting point of one of the metals; another remains as an unmelted constituent. An argon gas purge removes driven-off gasses and cools the furnace. For this particular piece of support hardware, Smith required a solenoid valve in the line and so he contacted New Jersey-based Automatic Switch Co. (ASCO).
ASCO's design process started with magnetic analysis performed in ANSOFT. The analysis allowed the supplier to optimize solenoid efficiency by reshaping magnetic, stainless-steel pole pieces. The final pole shape provided the force necessary to operate the valve in space.
The new design also combined the valve base with the solenoid base assembly. To accomplish this, ASCO replaced Smith's spec for 1/8-inch NPT connections with integrated stainless-steel tubing. This alone saved about 1 lb. of valve weight.
The valves were then machined and welded using a pulse TIG welder. This produced a hermetic seal, eliminating the need for O rings.
ASCO delivered eight solenoid valves within six weeks, and Smith's experiment functioned as expected during flight.
Plate design doubles bearing load capacity
Port Washington, NY- Thomson Industries' patented Super Smart Ball Bushing(TM)(SSBB) linear bearing series offers designers twice the load capacity or eight times the travel life of its older Super Ball Bushing(TM) (SSB) bearings. "We see this as a leapfrog technology in the world-wide linear bearing market," claims inventor Al Ng, chief engineer, Core Products.
SSBB bearings achieve greater performance by increasing the number of bearings and contact areas, and reducing friction. First, dual-track bearing plates with ball-conforming grooves replace single-track grooved plates. This roughly doubles the bearing count and maximizes the number of bearings in the load zone, which helps SSBB bearings handle full load capacity when installed in slightly out-of-round housing bores.
Second, the two-track, pivoting bearing plates self-align in roll, pitch, and yaw. To self-align in roll, the bearing plate's smaller outer radius rides against the larger radius of the ring. This allows it to roll against the ring and evenly distribute the load to each of its two ball tracks.
Pitch self-alignment occurs because the precision ring's convex undersurface allows the bearing plate to rock along the longitudinal bearing axis plus or minus 0.5 deg. This attribute assures smooth ball entry and exit in the load-carrying zone and optimum ball loading from end to end. It also compensates for misaligned housing bores and shaft deflections.
Each bearing plate also rotates about its center to prevent skewing of the ball tracks relative to the shaft (yaw). This minimizes friction and maximizes bearing life.
A comparison of equally sized SSB and SSBB bearings illustrates the SSBB's performance gains. A 5/8-in. bore SSB bearing has a 450 lb. maximum dynamic load capacity, while the same bore SSBB bearing rates 620 lb.; a 1.5-in. bore SSB bearing has a 2,000 lb. capacity, while the same bore SSBB bearing hits 3,880 lbs.
Ng believes his design will find many applications in motion control, such as pick-and-place devices, robotic arms, assembly machines, machine-tool guides, and ultrasonic welders.
--Russell King, Contributing Editor
Urethane tape reduces ambulance costs
Manasquan, NJ-Building custom emergency vehicles is very labor-intensive-and costly. But by using mounting tape to bond body panels on ambulances and similar vehicles, engineers at PL Custom Emergency Vehicles are reducing assembly time and improving reliability.
To bond the aluminum body "skins" to the tubular aluminum frames of ambulances and similar vehicles, PL engineers use a 0.030-inch-thick dense foam tape from Norton Performance Plastics Corp., Granville, NY. Norton supplies Normount(R) urethane tape with acrylic adhesive on both sides.
"Compared to welding or riveting, we're probably saving 40 man-hours per vehicle," estimates PL General Manager Robert Stevenson. The tape also eliminates the rework necessary to correct distortion caused by welding heat, and eliminates rattles and galvanic corrosion, say engineers.
The company first switched to liquid adhesives. However, mounting tape offers the advantage of needing only alcohol to pre-treat surfaces. "If we were still using wet mastic adhesives today, the VOC issue alone might be reason enough to switch," says Purchasing Manager Clifford Wooley. "Mounting tapes eliminate solvents in the mastic, and solvents to clean up the mess."
Replacing liquid adhesive with tape also reduces waste, such as unused cured adhesive, says Wooley, which lowers disposal costs. In addition, the switch eliminates the need to monitor shelf-life.
PL engineers estimate that the tape reduces production time by almost 20 hours per vehicle. Because it bonds instantly, assemblers can release the vehicles immediately, instead of waiting 24 hours for the adhesive to cure. "We can produce one more vehicle per week with the same crew and facilities," says Stevenson. "It's like a 20% plant expansion without any capital investment."
Because the vehicles are subject to severe outdoor environments, the foam's closed-cell structure adds reliability to the body structure by providing a moisture barrier. The foam also serves as a more effective vibration damper than previously used adhesives, claim engineers.
IBM boosts workstation, parallel- processing performance
Somers, NY-IBM has unveiled what it calls the world's fastest under-$40,000 workstation: the RISC System/6000 Model 3CT, rated at 266.6 SPECfp92 and 130.2 SPECint92 with optional cache.
The 3CT, built around a 67-MHz POWER2 microprocessor, boosts floating-point performance 30% over Big Blue's previous top-of-the-line desktop workstation. IBM is targeting the new machine for tasks such as structural analysis and electronic-circuit simulation.
The workstation comes equipped with 64 Mbytes of memory, a 1-Gbyte internal disk, POWER GXT150M graphics adapter, 32k instruction cache, and 128k data cache.
IBM also announced the Model 39H UNIX server, offering a 25% jump in speed compared to an earlier model.
In addition, IBM said it has designed the industry's first PowerPC-based X-terminal, the Xstation 160, featuring a PowerPC 603 microprocessor.
And, IBM beefed up its POWERparallel systems with several hardware and software enhancements, including an RS/6000-based processor for the IBM SP2 computer system. The Thin Node 2 processor features a faster data-flow design; IBM engineers say it provides up to a 40% enhancement over the earlier design.
Flexible software quickens design time
Windsor, CT-When designing a fuel-injection system, Diesel Technology, Wyoming, MI, faces the hurdle that injector moving parts must junction in a high- pressure environment. CAD helps engineers produce designs to overcome that problem.
Diesel Technology officials say the combination of CADKEY(R), DRAFT-PAK(R), and DMS-PRO(R) packages works best for its engineering design system.
The ability to switch from wireframe to surface to solid models, and back, all in 3-D, helps Diesel Technology develop design concepts more easily. "I do not want to have to be constantly changing en-tities into like types to manipulate the design," explains Design Engineer Diane Ellis. "We needed the flexibility, for example, of being able to trim a wireframe entity to a surface or to a solid, or a solid to a surface or to a wire frame."
CADKEY also helps by eliminating such steps as manually calculating the position of the holes to maximize wall thickness, and then cutting apart the fully machined bodies to check the design. Now Diesel Technology engineers just rotate the 3-D computer model to get the same information, according to Ellis.
CAD simplifies the transition from manu-facturing, too. "CADKEY's model-to-drawing associativity provides big savings in time here," says Ellis. "As we change things in model mode, the changes automatically show up in all the detailed views in the layout mode. You are always working in your model, and the changes appear in your detail."
After Diesel Technology decided to purchase CADKEY, they added DRAFT-PAK, a product of Baystate Technologies, Marlborough, MA, and DMS-PRO from the van der Rouest Group, Santa Ana, CA. With DMS-PRO, the engineers can develop fasteners, screws, and bolts in DRAFT-PAK, while keeping complete track of every part file's creation, modification, and location in DMS-PRO.
According to Harold Wieland, engineering design manager, the different software packages work so well together, it seems as if the same people designed them all.
About the Author(s)
You May Also Like