Engineering News 7378
May 8, 1995
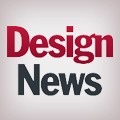
Design rescues products from the scrap heap
Newton, MA-Eastman Kodak Co., Rochester, NY, designs for recyclability and reuse. Others call it Design for Second Profitability, EnvironmentallyConscious Design, Life-Cycle Design, or Design for the Environment (DFE). Whatever you call it, environmental considerations in the concept phase of design stand to have a major impact on company profits and our natural resources.
"One of the certainties of life is death. Companies need a product design that is easily and quickly broken down," says Sandy Munro, president and product development consultant, Munro and Associates, Inc., Troy, MI. "In the future there will be penalties for products not easily scrapped-manufacturers will lose money if they don't deal with this now."
With legislative, financial, and awareness issues to face, many large corporations and universities are working to design products with the products' imminent demise in mind. Engineers are asking: How can this product be designed for remanufacturability, recyclability, or a combination of both? Cases in point:
Currently, 94 percent of all cars and trucks scrapped in the U.S. are dismantled and shredded, and 75 percent of their content by weight-including the iron, steel, aluminium, and copper-is recycled. Batteries, engines, transmissions, catalytic converters, and radiators are often removed and remanufactured or recycled.
Ford Motor Company's, Dearborn, MI, vehicle recycling program's two-pronged strategy uses materials from recycled products such as soda bottles in today's vehicles, while making the entire vehicle itself more recyclable. So far, more than 50 million recycled plastic soda bottles a year are finding new life as grille reinforcements, luggage rack side-rails, or door padding.
The 1995 Ford Explorer, Ranger, Contour, and Mercury Mystique are more than 80 percent recyclable. And Ford is not alone. Chrysler and General Motors offer examples of green design as well.
Many U.S. firms, such as Kodak and Xerox, Rochester, NY, view Germany's proposed legislation, requiring manufacturers to be responsible for disposing and recycling products at the end of the life cycle, as a sign of what lies ahead. So, engineers considering a design must look at manufacturing and service costs, and then beyond to the cost of disposal and recycling.
Products that are designed to be easier and cheaper to recycle or reprocess will keep companies in the black and ahead of their competition. Munro says that showing companies there will be a decrease in profit from their products in the future if they are not recyclable, will motivate them to move toward green design. "It will be in the future; this is not an "if' or a "maybe.' Green design is just a matter of time," he predicts.
Kodak offers a perfect example. In a program loosely modeled after soft drink company soda can returns, Kodak's single use camera recycling initiative salvaged parts and materials from 41 million single-use cameras. A snap-together, snap-apart design simplifies the part and material recovery process. Of the total number of "new' cameras shipped in any month, more than 75% are now returned for recycling. "We believe that for consumer recycling this program is second only to the soft drink industry," says Al Vandamore, Kodak's senior project engineer.
A small mark made inside each disassembled camera mechanism shows the number of times the camera has been recycled. Many cameras now bear five marks.
In fact, Kodak reuses up to 85% of the parts, claims a company spokesperson. The design of the camera makes it possible to reuse much of the camera without fully disassembling it. The paperboard outer shell is burned in a waste-to-energy incinerator. Kodak grounds up other parts of the cameras that don't pass inspection and adds them into the raw material stream for molding into new cameras, significantly decreasing need for virgin plastic.
The Kodak initiative is a closed-loop system. The cameras are sealed so consumers must return them to photofinishers to have their pictures developed. Kodak reimburses photofinishers five cents for each camera returned and pays all shipping costs.
Another natural. Xerox also is serious about design for recycling. According to Patricia Calkins, manager, resource conservation projects, "Re-manufacturing engineers work with product design teams to design for remanufacturability. There's a drive towards waste-free products."
One example of recycling and remanufacturing at Xerox involves
the 5028F Copy Cartridge. When old cartridges are returned either by customers (a self-addressed, post-paid return envelope is pro- vided with each new cartidge) or technical representatives, they are disassembled. Xerox reuses or recycles about 97% (by weight) of the parts and assemblies. For example, the company grinds up plastic parts and reuses the resin.
Most Xerox products are returned and remanufactured, including the 5018, 5028, 5328, and 5334 copiers. In fact,Xerox designed the 5021 to use up a surplus of 5018 and 5028 hulks.
"We want to get to the important components. They are designed to come apart so we can replace worn parts and reassemble to new machine quality and reliability standards. These machines are not refurbished. There's a full warranty because they function like a new machine," says Calkins.
Work progresses at the university level as well. Last autumn, Samsung Electronics Corp. of Korea awarded University of Rhode Island's (URI) Industrial and Manufacturing Engineering Department (IME) a contract for product redesign studies in the area of Design for Disassembly, Service, and the Environment. According to Winston Knight, professor and chairman of the IME program, the research entails looking into the disassembly and total life cycle analysis of three Samsung appliances.
Fewer parts. In a separate project, Booth-royd-Dewhurst Inc. (BDI), Wakefield, RI, Consultant and URI Professor Geoffrey Boothroyd and his research assistant, Anthony Girard, modified the design of a coffee maker to incorporate fewer parts, making it easier and faster to disassemble. The next step consists of making the most valuable parts also the most accessible parts.
BDI Design for Manufacture and Assembly (DFMA)(R) software assisted in appliance disassembly early on in the program. BDI has taken the information collected so far and applied it to a preliminary Design For Environment software package. This work should lead to a Beta version of DFE software targeted for testing in late 1995 or early 1996.
The URI researchers encourage engineers to consider disposal when designing products. They also warn that early in the design cycle engineers must consider whether combinations of materials and/or assembly processes will seriously impact the cost of , or even prevent, recycling efforts. For example, although the marking of plastics for recycling is becoming widespread, this may be to no avail if different plastics (or different colors of the same plastic) are used with assembly methods that render separation difficult or impossible. Similarly, such items as labels, surface coatings, adhesive, and paints applied to plastic parts, may make them difficult or impossible to recycle.
Nabil Nasr, assistant professor of Industrial Manufacturing and Engineering Department, Rochester Institute of Technology (RIT), agrees that designers must be aware that when they combine materials, it can make recycling costly, difficult, and, sometimes, not even feasible. "If the customer asks for a certain kind of paint, the customer needs to be made aware of the problems at the recycling stage," explains Nasr.
"As a product is being used you have to replace units, but at some point you reach the retrieval stage, where product life is over. There are three options: disassembly, recycling, remanufacturing. Ultimately we are trying to establish design practices that make remanufacturing possible," continues Nasr.
When reliability is achieved in a green design, engineers will not only help the planet, they will provide companies with new sources of revenue and a positive public image.
3-D software helps slash computer design time
Calabasas, CA-Solid modeling has cut product-development time by at least 33% at S.G. Hauser and Associates-and allowed engineers to tackle more ambitious designs than ever before. "The fact is, we wouldn't even attempt some of these projects if it wasn't for solid modeling," says Ron Pierce, vice president at the design firm.
Hauser recently used Hewlett-Packard's SolidDesigner software for the first time on a computer project for IBM and 3M. One result: They slashed prototyping time by more than 60%. The software allowed designers to more easily work with the complex curves they wanted for a more dramatic look. "The Panda project simply could not have been done any other way," says project manager Edward Cruz.
The Panda went from concept to working prototype in about two months. And, manufacturing processes, which used to take weeks, were cut to days. For example, the aluminum computer base was manufactured by a CNC vendor in one day; previous methods took at least two weeks. "The form and aesthetics we were after couldn't have been realized in production if we couldn't generate those compound free-form shapes in the 3D solids program," according to Cruz.
Prototyping time was further cut because some test-ing, for things like fit and finish, was done on the computer instead of building physical models.
Design engineer Vince Razo says his 3D models captured complete analytic and free-form geometry, as well as design information, such as dimensions, attributes, and instructions. This made it easier to move accurately from design to reality. "What we saw on the screen is exactly what we got," he says. "The parts we did for Panda were 100 percent, dead-on accurate."
Segmented stator yields compact servo motor
Tokyo-To create an ac servo motor one-third the size of conventional motors without sacrificing output, engineers at Matsushita Electric's Industrial Motor division went against the trend toward parts consolidation. Central to the compact "Minas" motors' size advantage: A segmented stator core.
To develop compact, high-density windings, the stator core of the motor is segmented into 12 units, rather than a conventional single stator core. Because each stator segment is individually wound, the segmented stator yields higher-density windings than are possible with a single stator core. After soldering and inspection, a laser-welding technique bonds the core stacks. The technique is patented in the U.S., Japan, and Germany.
A high-energy magnet and compact encoder complete the Minas design. The smaller motor means smaller end-products, and close-packing the layer elements for stamping reduces scrap by as much as 10%, claim Matsushita engineers.
Plastics recycling research facility opens
Berkeley, CA-Anyone traveling in the vicinity of Berkeley, CA, and interested in the latest developments in plastics recycling should make it a point to visit a just-opened research facility built by MBA Polymers, Inc. with a grant from the American Plastics Council (APC).
The new facility, the second such operation partially funded by APC, will focus on advanced mechanical recycling technologies, including:
Increasing throughputs.
Lowering operating and capital costs.
Improving cleanliness and purity of recycled plastics.
Developing separation techniques.
The facility's pilot line incorporates various stages in a sophisticated recycling process. A size-reduction operation can accommodate foreign materials, such as metals. A state-of-the-art, three-stage air classification system can produce up to four different streams using only air. An innovative low-energy, high-throughput wet grinding operation is also part of the system.
The remainder of the line works like this. Once properly sized, the materials pass through a series of hydrocyclone systems to remove any residual foreign material and separate plastics by density.
Video system captures high-speed events
Dayton, OH-Environmental concerns recently forced engineers at Air Force's Wright Laboratory to evaluate alternatives to Halon 1301 as a fire-suppression chemical. To appraise the performance of potential substitutes, they needed a high-speed video system capable of withstanding the inferno-like conditions of the test fixture.
The substitute chemical, which will be used in aircraft dry bays and engine nacelles, will operate at temperatures of -65 degrees F to 250 degrees F. It must be able to snuff out fire in a fraction of a second under air flows as high as 450 mph.
Wright engineers teamed with Synergy, Inc., Dayton, OH, to set up the test site. To record fire-extinguishing exercises and evaluate the pattern of the flame as it was put out, engineers chose a high-speed on-line video system from NAC Visual Systems, Woodland Hills, CA. The HSV-1000 required no customization for the application, say Synergy engineers.
The system's main benefits are 640- x 480-pixel resolution and color high-speed video recording at 500 and 1000 frames per second, says NAC product manager Jim Lafer. The recording system uses a drum with four recording heads. It takes an analog signal from the sensors, process it digitally, then converts it back to an analog/tape signal. The system is available world-wide and meets German and U.S. electrical standards.
The Air Force plans to have a Halon replacement in use this year. The U.S. Army, Navy, Federal Aviation Administration (FAA), and auto-racing associations such as NASCAR also are using the system to evaluate Halon alternatives.
"The video system can be used to record anything moving too fast for the human eye to comprehend," says Lafer. Additional applications include vehicle crash research and investigation of manufacturing problems.
Stealth station wagon rules the road
Dana Point, CA-If you were driving the highways of Orange County earlier this year and a yellow Volvo wagon streaked past you at 110 mph, that was probably me. I had no idea I was going that fast until my passenger noted the shocked looks of the sports car drivers we left in the dust.
I was driving Volvo's special edition of its 850-the T-5R. It features increased horsepower and tauter road handling. Also on board are all the goodies you could hope for: Pirelli 205/45 ZR 17-inch tires mounted on 7 x 17-inch 5-spoke alloy wheels, dual front-seat heaters, 8-way adjustable front seats with three memory settings, trip computer, and a slide glass sunroof.
"Volvos had lacked performance, sportiness, stylishness. Our image was as a safe, durable, reliable, spacious family carmaker," says Wil-liam J. Hoover, Volvo executive vice president. "With the T5-R we put safety first-note the driver- and passenger-side front and side airbags-then added style and performance and made it fun to drive."
The T-5R's engine maintains the same in-line, 5-cylinder architecture as the 850 Turbo, but it cranks out 240 horsepower, compared with its 222-hp cousin. Engineers accomplished this by reprogramming the engine-management system to increase Turbo boost from 9.6 psi to 10.9 psi during full-throttle acceleration. The increased pressure lasts 7 seconds at 5,600 rpm. Other specs include 221 lb/ft of torque at 2,100 rpm, 19 mpg in the city, and 26 mpg on the highway.
The T-5R comes as a sedan ($35,500) or a wagon ($37,000). Both are available only as 4-speed automatics in North America, and there will be only 1,000 of them to go around.
An advanced Traction Control System provides anti-wheel spin control through the ABS, and works to help reduce front-wheel spin at speeds of less than 25 mph to enhance both traction and steering control. Also, an up-rated sport suspension consists of larger stabilizer bars and heavy-duty hydraulic (sedan) or self-leveling (wagon) shock absorbers. These features-along with the 17-inch wheels and meaty tires-greatly improve road performance and create the most aggressive appearing Volvo ever built, company officials say.
Although I found the steering a little mushy, the ride was remarkably smooth. I spent time driving on curvy mountain roads, but felt secure and probably drove faster than I should have. And I must admit, I didn't feel like I was driving a staid family car.
Volvo says it won't be going to the jelly-bean shape any time soon. Hoover says the company will be evolving its style slowly, adding some rounding, but keeping certain unique Volvo characteristics. "We can still draw a straight line."
Plastics-identification technology debuts
Detroit-The American Plastics Council (APC) has endorsed a fast identification system based on a mid-infrared technology that can classify at least 23 different types of plastics. The announcement, made at this year's SAE International Congress and Exposition, could open the door to expanded plastic-recycling operations, particulary in the automotive industry.
The equipment, P/ID 28, is produced by Bruker Instruments, Inc., Billerica, MA. The three-foot-tall, semi-portable instrument can read the "fingerprint" of virtually any plastic sample. Using reflected light, plastic parts held up to the instrument are "scanned" and identified within five seconds.
Unlike other infrared identification equipment previously evaluated, this system can identify black-colored plastics, and requires minimal sample-preparation time. Modifed specifically for use with plastics, the equipment is said to be highly reliable and easy to use. It will soon be available to recyclers, material suppliers, labs, and other entities involved in recycling.
Following its SAE introduction, the instrument was moved to the Vehicle Recycling Development Center in Highland Park, MI, where it will undergo more evaluations before being sent out for added field tests. The research facility operates under the Vehicle Recycling Partnership, one of 13 cooperative efforts by Chrysler, Ford, and General Motors.
Computerized control system weaves a new niche
Ringold, GA-Compared to conventional looming, the tufted-carpeting process provides high quality carpeting at high production rates with less setup time. But as a trade-off, this process rarely allows for mass production of carpets with complex patterns. So, tufted carpeting rarely comes in any styles other than single, solid colors.
Recently, Tapistron International and Berkeley Process Control, Inc. joined forces to produce a tufting machine that could produce carpets with complex patterns. The result: the Computerized Yarn Placement (CYP) system that now incorporates a machine control system instead of a multifold system of cams and gears.
Specifically, servo motors controlled by Berkeley's Cam Profiler option replaced the CYP's mechanical cams. This new system provides the ability to define and adjust multiple cam profiles electronically.
"Complex patterns could require the control of up to a thousand cones of yarn," says Tapistron's Jonathan Bragdon. "Adjustments to the CYP can now be made in seconds, at the press of a button."
The application required up to nine different servo axes to impose a high-speed, cam-like motion on needles and other machine implements. This had to be done while hundreds of I/O devices were synchronized to deliver specific colored yarns at precise points in the path of each needle.
Using Berkeley's Bam-832hT machine controller, Tapistron accomplished this task. Since the controller's operating system is priority structured, says Berkeley, crucial tasks like servo control and solenoid actuation take precedence over less time-critical functions like data entry.
To ensure proper machine operation, operator controls were implemented by Tapistron using Berkeley's Panelmaker(R) Development System and touch-sensitive operator interface. Bragdon notes that this made the loom's operation more intuitive.
Axis-positioning modules provide top-notch control
Somerville, NJ- When Metal Conversion Systems (MCS) needed to design a wire-slitting machine with precise winding and speed, the company decided PLC control was best. Installing several of GE Fanuc's Series 90-30 PLC's on the machine, MCS "enhanced product consistency and increased the machine's manufacturing speed by 60%," says John Smero, VP and co-partner of the 11-year-old company.
The 40-ft long machine accepts coils of unprocessed clad material. The material, once fed through a payoff bridle infeed section, travels through three scoring heads which part it into 13 separate strands. The 13 strands are then directed to 13 separate spools.
Smero states that the 90-30 PLC, with its axis-positioning module (APM), was selected for its following mode and electronic gearing control. Fifteen single-axis APMs have been configured in the follower mode-13 on the winder and two on the slitter.
According to Stan Smero, control engineer at MCS, the PLC sets and controls line speed by altering an analog output to the motor drive for the material going out of the exit slitter. This information is then fed from the exit slitter into a pulse generator which, in turn, feeds a signal to the entry and center slitter's two APMs.
These entry and center slitters are geared at lower speeds to maintain a certain amount of tension between them. Both slitters, which are in the follower mode, run at a tension rate between 80% and 90% by the time the material is ready to exit.
At the winder end, 13 traverse winding units move the spools while the material stays straight. Each of the 13 APMs then controls the motion of the 13 individual winding units.
Because material widths vary from 0.040- to 0.250-inch, programming was particularly complicated, says Stan Smero. Smero solved the problem by connecting the .25-hp dc drives to the 13 APMs for drive control.
Smero is also feeding the 13 APMs with signals from two feedback pulse generators. One acts as the master on the spool to count the number of times a spool makes a revolution, and the other provides position feedback of the spool in the traversing sweep.
The 90-30 PLC then calculates how many pulses go in one direction before going the other way. The width of the material and gap is used to calculate how far the winder has to move relative to speed rotation.
Says Smero: "All 13 winder APMs with their 13 inputs and 26 outputs start at the same time, every time, and have not strayed beyond 0.002 of an inch."
IBM's "Butterfly' turns heads
Somers, NY-Computers generally win attention with things like blazing speed or jazzy multimedia. However, the head-turning feature on IBM's hot new notebook PC is a part of a computer not normally in the spotlight: its keyboard.
IBM's ThinkPad 701 incorporates a fold-out, near-full-size TrackWrite keyboard that is winning rave reviews.
"This is by far, the best keyboard on earth," Kimball Brown, a Dataquest Inc. analyst, told the Reuter news service. Adds Bill Ablondi, vice president of BIS Strategic Decisions: "IBM has blown the lid off the mobile computing market."
Codenamed "Butterfly" while under development, the ThinkPad 701C measures 9.7 x 7.9 x 1.7 inches and weighs 1.7 lbs. When it is opened, two keyboards spread out and interlock to form a keyboard almost two inches wider than the unit itself, with 85 keys. It was invented by a team headed by John Karidis at IBM's Thomas J. Watson Research Center, Yorktown Heights, NY, and developed with another team at IBM's Research Triangle Park, NC facility. IBM officials believe the keyboard offers such a competitive advantage, that they will not release drawings showing how the device unfolds.
The ThinkPad 701C also includes a 10.4-inch diagonal active-matrix screen, and infrared capability to send files to printers and other devices supporting the Infrared Data Association standard for wireless data transmission. It comes with built-in speakers, microphone, 14.4 kbps data/fax modem, Intel 486 CPU, and IBM TrackPoint pointing device.
An IBM spokesman says the company's PC division received more pre-production orders for the Butterfly than any product in its history. Prices start at $3,599.
Wobble motor goes miniature
Tokyo-Matsushita Electric Industrial Co. recently developed a fabrication process that yielded a prototype electrostatic wobble motor just 15 mm long.
The wobble motor, with an outside diameter of 1.4 mm, uses a concentric build-up process that borrows from silicon micromachining techniques.
The assembly process begins with a cylindrical substrate used as a rotor shaft. RF magnetron sputtering adds a rotor electrode to the shaft, then an insulate layer. This is followed by a dip-coated sacrificial layer of polyimide film. Next, stator and ground electrodes are plated on the sacrificial layer.
After the wire bonding process, an insulating resin fills the spaces around the electrodes to isolate them. Finally, solvent removes the sacrificial layer to separate the rotor from the motor casing.
The motor operates from 350V pulses and rotates as fast as 140 rpm with an applied excitation of 14k pulses/sec, say Matsushita engineers.
Micro PLC decentralizes conveyor control
Newton, MA- Wes-Tech Automation, Buffalo Grove, IL, recently re-designed its Tech-Trak modular conveyor system so it is easier to assemble and use.
Tech-Trak(R), which features a variety of tracks and switching stations, allows users to quickly reconfigure components in response to changing materials-handling needs. It originally employed a central programmable logic controller (PLC) with a relatively large number of inputs and outputs (I/O) to an conveyor's sensors and actuators. Distributing that control to the various modules would simplify wiring and control-system programming.
"We have eight different conveyor modules and each requires a different set of logic," explains John Vales, controls and electrical department manager at Wes-Tech. An initial attempt at distributed control used custom control boards for each module. Dedicated control boards enhanced the modularity of the conveyor system, but they were costly and inflexible. Says Vales, "We couldn't adapt them to any of our other systems."
The system now uses FX0 micro-PLCs from the Industrial Automation Division of Mitsubishi Electronics, Mt. Prospect, IL. Beyond eliminating the cost of building unique circuit boards for each module, the FX0 allowed Wes Tech to off- load specific control functions performed by the central PLC. As a result, I/O needed by the PLC decreased, reducing panel-space requirements by as much as 30%.
On individual modules, the micro PLCs handle functions like pallet stops and turn gates that were previously controlled by the central PLC. The new control scheme thus minimizes the need to route cable and wiring from the central PLC to the local conveyor modules for further cost savings.
Stepper motor/driver gives microscope an edge
Chatsworth, CA-McBain Instruments developed what it calls the first-of-its-kind motorized industrial microscope column using the Nanostep motor/driver from Oriental Motors, Torrance, CA. McBain engineers replaced manual controls with electronics to simplify the design and make the unit easier to use. They chose the motor for its low vibration and less audible noise.
The Nanostep is a 5-phase, high-resolution motor/driver package with extremely quiet operation. The driver provides smooth rotation through 16 user-selectable resolutions ranging from full step up to 250 microsteps per full step, or 125,000 microsteps per motorshaft revolution.
The Pentagon drive method used in the Nanostep operates about 10 to 12 dBa lower than standard motor drivers, according to Oriental. This is due to the elimination of vibration noise and audible chopping noise. The drive power capability of the unit is 24V dc and up to 1.4A per phase.
The ZIII's predecessor used separate gearbox-driven manual coarse- and fine-focus mechanisms and a rigid crossed-roller bearing guideway. However, the manually driven device required that the operator reach forward and up to use the focusing mechanisms, movements that could result in fatigue or discomfort. Attempts to mechanically "remote" these functions were awkward and visually unappealing, the company says, so McBain decided to motorize the focus axis using small dc motors or 2-phase steppers.
"The dc motors were inexpensive and relatively smooth in operation, but they had a propensity to drift over time," says Craig Goff, McBain manufacturing manager. "The 2-phase stepper approach was more expensive, but the stepper would sit still when left at a given commanded position." However, the stepper was rough, noisy, and "notchy" as it traversed throughout focus.
"The 5-phase Nanostep is a much smoother, quieter device than the 2-phase units," says Goff.
The microscopic column can be used for high-tech work involving tolerances in the micron or submicron range, such as inspecting silicon wafers, fiber-optic ends, and biomedical devices.
Low-cost bearing stabilizes valve
Exeter, CA-When engineers at Waterman Industries, Inc. developed a lower-cost alternative to its line of heavy-duty butterfly valves, they needed a plastic bearing for the stainless-steel shaft within the valve's cast-iron housing.
Reinforced nylon bearings, produced by a local injection molder for the prototypes, couldn't maintain the dimensional control stability that was needed. "There was too much variation in the molded product," explains Jim Pyles, a Waterman manufacturing engineer who developed the line of Waterman VBE2 Valves. A plastic bearing from igus, inc., East Providence, RI, provided a low-cost solution.
Designed for agricultural use, the Waterman VBE2 valve typically joins two pieces of irrigation pipe to control the flow of water through a line. Inside the valve housing, a rotating disc is fitted to a stem, which opens and closes the valve by means of an operator-for example, a hand wheel or manual lever. Bearings made of igus' iglide(TM) G300 material were selected for this particular valve application.
The material consists of a wear- resistant thermoplastic alloy base, a network of long composite fibers, and a mix of solid lubricant, which homogeneously impregnates the material. The fibers provide high strength (21,750 psi tensile strength), and resistance to compression (compressive strength of up to 11,600 psi).
The solid lubricant offers excellent anti-friction and low-wear properties. There is no need for a separate lubricating film or coating found with metal bearings.
The G300 bearings are totally resistant to alkali solvents and to most moderately strong organic and inorganic acid solutions. The material also offers excellent abrasion resistance.
Iglide bearings are designed to be press fit into the housing, without special tools or lubricants. The self-lubricating property of the bearings provides a distinct advantage over metal bearings that are typically pressure-lubricated through a hole in the journal that houses the bearing.
Oil and other lubricants can become contaminated with dust and solid contaminants, reducing the bearing's performance life. These oil-free iglide bearings require no additional lubrication and they are totally maintenance-free, which further reduces operating costs.
Waterman's VBE2 valves are offered in fives sizes to fit pipes of four to 12 inches in diameter, for applications that use a maximum operating pressure of 150 psi. The product consists of a stainless-steel stem, cast-iron body and disc, and a replaceable, one-piece rubber seat-ring that seals the disc and stem. A manual level is standard.
Since its introduction, sales of the economy butterfly valve have been increasing. Pyles reports that the valve is more expensive than offshore competition, but it is also going to last a good deal longer. "Compared to imports, we are making a higher quality valve. And that's our niche."
About the Author(s)
You May Also Like