Electrohydraulics control truck's wheel slip
January 9, 1995
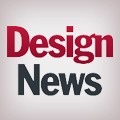
Butler, WI--By adding an electrohydraulic circuit to a truck's braking system, engineers have created a new type of traction control.
Used on Euclid Hitachi 60- and 85-ton off-road trucks, the new system is important for the off-road large-vehicle market. Such trucks typically don't come with limited-slip differentials. As a result, most have no way of directing power away from a slipping wheel.
The new system, however, changes all that. By employing a fast-acting electrohydraulic valve, engineers at Apitech, a Unit of Applied Power, Inc., enable the truck's braking system to perform traction-control duties.
Other Applications |
|
To achieve this objective, the system employs a set of sensors, a microprocessor-based controller, and an extra hydraulic-valve manifold. The valve manifold mounts atop a brake manifold, which splits the system to independently activate brakes on the vehicle's left and right sides.
During operation, the controller "looks" for slippage at the wheels. To find slippage, it counts magnetic pulses generated by gear teeth on the truck's axle. When wheel rotation on the left and right sides of the vehicle exceeds a programmed slip ratio, the controller signals the electrohydraulic valve.
Controlled by the microprocessor, the electrohydraulic valve sends a control pressure to a reducing valve in the braking system. The control pressure acts as an input to the reducing valve, thus proportionally controlling its output. As a result, the electrohydraulic valve modulates the brake's clamping force according to need.
By operating in this way, the brakes act as a traction-control system. When the left rear wheel begins to slip, for example, the left rear brake applies clamping force. As it operates, engine torque is automatically directed along the path of least resistance--in other words, to the non-slipping wheel. Result: Power is transmitted to the wheel that can move the vehicle.
Key to the new system is the use of Apitech's electrohydraulic proportional valve. The valve, which responds in 5 mseconds, quickly supplies a control pressure. "The valve acts very quickly to generate a proportional signal," notes Feng-Rong Shaw, manager of electronics and systems engineering for Apitech. Its short stroke and large internal area make the valve's fast response possible, Shaw says.
Using the electrohydraulic valve, the system's complete response time--starting with the sensor pick-up and ending with the braking force--is about 0.1 second.
Apitech engineers say that they could have achieved some of the same capabilities with a servovalve. But a servovalve would add cost, size, and weight to the system. "Here, we use a simple spool valve that is very compact," says Alan Crow, managing director of mobile equipment systems for Apitech. Servovalves, he says, would also have been more susceptible to contamination problems in harsh, off-road environments.
For off-road drivers, the traction system offers simplicity and greater control. In the past, weather was a critical factor for operators of heavy off-road vehicles. Drivers of 60- and 85-ton off-road vehicles could not operate their machines in slippery conditions. "If there was rain or mud on the ground, you just didn't run the truck that day," notes Ron Schantz, senior project engineer-hydraulics for Euclid-Hitachi Heavy Equipment, Inc., Cleveland, OH. "This system allows the vehicles to be more productive."
Additional details, electrohydraulic valve...Contact Feng-Rong Shaw, Apitech, a Unit of Applied Power, Inc., Box 501, Milwaukee, WI 53201, (414) 783-9406.
Additional details, heavy off-road trucks...Contact George Kenyon, Euclid Hitachi Heavy Equipment, Inc., 22221 St. Claire Ave., Cleveland, OH 44117-2522, (216) 383-3377.
About the Author(s)
You May Also Like