Application Digest 24426
June 26, 1995
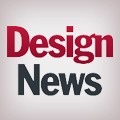
Simplified Magnetic Measurements Cut Costs
By Gordon Ross, Design Engineer, Honeywell Inc., Micro Switch Division
Reducing operating costs is a goal most companies work on continually-for their customers as well as for their own organization.
Design engineers focus specifically on finding cost-effective applications. On a more specific level, using a simple bench set-up can help you evaluate possible Hall-effect sensor applications. Applications using Hall-effect sensors can include but are not limited to bin-level control, joystick applications, ignition timing, position sensing, and vibration sensing.
Engineers can use a linear Hall-effect sensor instead of a gaussmeter for concept tryout in magnetic designs. This may be desirable for a number of reasons: lack of a gaussmeter, limited space, lack of modeling capability, or the need for a disposable probe. A linear Hall-effect sensor such as the SS94A2D from Micro Switch can be used as the sensing element. This will sense the magnetic field perpendicular to the surface.
Connect the linear Hall-effect sensor to an 8V dc power supply, which will give a meter reading of 1 mV/gauss. Adjust the trimpot so that the meter reads zero with no magnetic field present. The meter now will read 1mV/gauss for magnetic fields of -2500 gauss to +2500 gauss. If you're using a linear Hall-effect sensor with a sensitivity other than 1 mV/gauss, you'll need to divide the meter reading by the Hall-effect sensor sensitivity. Replace the voltmeter with an oscilloscope if you're measuring a changing magnetic field.
To speak with a Micro Switch applications engineer, call (800) 366-6786.
Analog Design Prevents Pointing-Device Drift
Melody Williams, Program Manager, Keyboard Division, NMB Technologies Inc.
Some notebook computer manufacturers using pointing-stick devices express concern about problems associated with strain-gauge pointing sticks.
Movement of the cursor on the screen when there is no touch to the pointing stick is called "drift." Drift may be caused by temperature change or by electrical noise affecting the pointing-stick circuit. The electrical noise may cause drift directly or defeat the algorithms that normally correct for slow changes.
Temperature change can occur either on the strain gauge itself or in the internal electronics. Temperature change occurring on the stick may cause the resistance to change if it influences only one of the strain gauges. Temperature change of the electronics due to heat inside the computer will also cause a change of input voltage. This change of input voltage will result in very small cursor-movement signals-less than one pixel.
The transfer function of the pointing stick, which is the translation of force to cursor movement, is structured so that forces less than several times the smallest force that can be measured result in no cursor movement. Therefore, the system detects slow changes and corrects them before any cursor movement is generated. To accomplish this correction, the software must distinguish between the signal caused by temperature change and the signal from a user's finger on the stick.
To make the distinction, the system looks at the steadiness of the signal. Temperature changes are consistently slow and steady, while a user's finger produces relatively rapid, not perfectly steady inputs. When the controlling software "decides" that the stick is not being touched, it recalibrates to a "zero" or "hands off" condition.
Excessive electrical noise in the circuits can defeat the software. Because the signals involved are only on the order of a few tens of microvolts, electrical noise interference can be avoided by good analog design work. Such designs require isolation of low-level signal nets and ground planes, careful grounding, and a reasonably stable power supply.
To speak with an NMB applications engineer, call (800) 662-8321.
About the Author(s)
You May Also Like