Application Digest
May 22, 1995
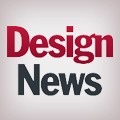
Designing plastic gears to last
Tody Mihov, Application Engineer, Intech Corporation
Plastic gears, when properly designed, offer many advantages compared to metal gears. We have found out the hard way, however, that the Lewis formula most engineers use to design metal gears will cause problems when applied to plastic gears. Differences in the characteristics of metal and plastic can lead to skewed results.
Having tested alternative plastic materials, Intech engineers identified Power-Core(TM) gear material, a Lauramid(R) composite cast around a metal hub, as a material that exhibits superior stability over time and carries high loads under varying conditions.
Usually, prototype parts must be fabricated and tested to define the point of failure. At Intech, however, formulae empirically derived during 10 years of experimentation with a complete range of gear sizes give our engineers a unique ability to predict gear life for INTECH Power-Core. The formulae apply at a wide range of rotational loads and speeds, with and without lubrication.
Gear calculation for Power-Core gears does not require including backlash to compensate for swelling due to moisture absorption. Also, the metal hub used in our gears reduces thermal expansion. In short, the high accuracy of gear machining, and the fact that the properties input to the gear calculation do not change significantly during the gear's operation, make our software a reliable predictive tool.
For application help with INTECH Power-Core(TM) Lubrication-free gears, call: (201) 767-8066.
Improved Spring-Pin Performance
Michael J. Dagle, Coiled Spring Pin Product Specialist, Spirol International Corp.
Providing uniform stress distribution and an ability to absorb shock and vibration, the coiled spring pin offers design engineers the option to select from three different types (standard, heavy, and light) to satisfy a broad range of application requirements. This choice enables an engineer to more effectively control loads imparted to hole material by the coiled pin, both during installation and while the pin is in place.
When you use coiled pins, compression during installation starts at the outer edge and moves uniformly inward through the coil. Consequently, the pin absorbs applied load more readily. Broad distribution of shock and load also minimizes stress points and makes the pin ideal for fatigue-related applications.
The compressibility or "give" associated with coiled pins accommodates greater hole tolerances than other types of pins. Also, the radial tension generated during installation sustains a tight fit that ensures the integrity of the assembly.
With their unique spring flexibility, coiled pins offer several specific and significant advantages: Elimination of distortion, cracking, and breakage around the hole; relatively low insertion forces; shock and vibration absorption; long-term assembly integrity; radial and longitudinal conformity to accommodate hole variations; compatibility with automatic-feed systems.
The coiled spring pin was developed by Spirol International, headquartered in Danielson, CT. The company remains the major manufacturing source.
To speak with a Spirol applications engineer, call: (203) 774-8571.
About the Author(s)
You May Also Like