At NPE2015, Transparent and Plastic Klear Can Looks to Eat Away at Metal
March 23, 2015
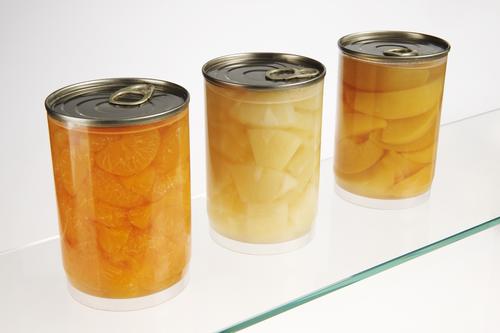
Of the products and technologies on display at the NPE2015 plastics expo in Orlando, Fla., this week, one in particular could dramatically change segments of food packaging. Injection molding machine maker Milacron is showing Klear Can, a transparent plastic can with a metal top and pull tab for fruits, vegetables, and meats that competes with metal cans.
Klear Can is a three-layer, co-injection molded structure of polypropylene (PP), for the inner and outer layers, and ethylene-vinyl alcohol (EVOH) as the barrier core. The can holds 410 mL of product, is 1 mm thick, and weighs 26 grams - 40% to 50% less than metal cans. The structure withstands retort of 130C. Depending on the amount of EVOH -- typically 5% to 10% -- shelf life is two to five years.
The global consumption of metal food cans is 50 billion units annually. But, as plastics have repeatedly done in the past, the novel plastic can could take a bite out of that market. "This is an opportunity for plastics to take a share of a metal market," Russell Bennett, Milacron's vice president of sales and marketing for co-injection technology, said.
Brand-holders like the can, he adds. Its appeal is transparency. "The feedback from potential customers is that a transparent can is a perfect can," Bennett said. "Brand-holders are interested in showing food at the point of sale."
MORE FROM DESIGN NEWS: NPE2015: 5 Must-See Exhibits
Although PP does not have good transparency, developments by Milliken & Co. in clarifiers -- plastics additives that enhance clarity -- significantly improve the visual impact of PP.
Another plus is that the container runs on conventional canning lines for filling and application and sealing of the metal top. It can also be processed with conventional retort equipment.
MORE FROM DESIGN NEWS: Would You Wear a Dress Made From a Yoga Mat?
On the molding line, all three layers of the container wall are injected simultaneously, rather than sequentially, for uniform barrier distribution. Milacron supplies the "hot half" of the mold, which splits resin flow. The "cold half," with the mold cavities, can be produced by any moldmaker.
At NPE2015, a four-cavity mold that produces cans in eight-second cycles will be shown. A 32-cavity stack mold (16+16) has been built for higher production volumes. The smaller mold runs on an injection molding machine with 280 metric tons of clamp force; the stack mold needs a 650-metric-ton unit.
Features of the Klear Can include a proprietary "false-foot" design to prevent deformation during retort. A dome-shaped panel flexes out to maintain the shape of the can during cooking. When contents cool, the dome retracts.
Kortec, a packaging specialist in Rowley, Mass., developed the Klear Can and first showed it at Interpack 2014 in Germany. Milacron acquired Kortec last year.
Pat Toensmeier has more than 30 years of experience writing for business-to-business publications. His main areas of coverage have been defense, design, manufacturing, technology and chemicals, especially plastics and composites. He has reported extensively on developments in these areas from the U.S. and Europe, and covered industry events as well in Brazil and Asia. Toensmeier has held various positions at major publishers such as the McGraw-Hill Companies and Hearst Corporation. A graduate of the University of Missouri, he is a contributing editor for several print and online publications. Toensmeier is based in suburban New Haven, Conn.
About the Author(s)
You May Also Like