Mechatronics Boosts Productivity on Photo Kiosk
February 7, 2007
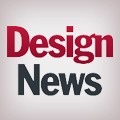
Thanks to a mechatronics-based approach, Boston Engineering developed time- and cost-saving design options for its new digital photo kiosk.
The kiosk uses an innovative printing process that allows customers to instantly print images from digital camera files. The key to the success of the product lies in maintaining a high print quality in images. This requires precise tension control of media spools. Engineers need to design a tension controller that could adjust to vibrations from the cutter head, the varying number of photos printed at a time and variances in speeds of the motors driving the device.
In addition, the development of the control system for the kiosk demanded ongoing, cross-domain consultation among mechanical engineers, hardware designers, software developers and those knowledgeable about the details of the application. Knowing that careful modeling and prototyping was important for a successful design, Boston Engineering used higher-level computer tools for electromechanical design, as well as for modeling the controller and prototyping the system.
Engineers first created a CAD model of the mechanical system using SolidWorks. Designing the CAD model allowed the initial work on the mechanical details to be performed virtually. The mechanical modeling required several iterations, while the customer better defined the subsystem mounting and volume allocation. The bandwidth and margin criteria, together with cost and weight targets, further refined the mechanical model.
The next step was to design and simulate a sixth-order control algorithm required to meet the system's closed loop bandwidth of 20 Hz. Once the simulation showed that the system could meet the design specifications, engineers created a physical prototype.
To develop the prototype, Boston Engineering relied on National Instruments' LabVIEW graphical programming environment and CompactRIO, which is NI's FPGA-based rapid prototyping hardware platform that features a controller and modular I/O.
The engineers turned to LabVIEW to program the supervisory program on the module's embedded microcontroller and also to implement the motor control algorithm on the FPGA. This approach provided a similarity in programming model between the prototype and the end system. Besides controlling the two motors, CompactRIO provided pulse-width modulator (PWM) outputs to control:
Encoders that provide velocity feedback for the motors
Analog input channels for the Hall-effect sensor to detect position
Digital lines for signaling
Channels for thermal and air readings
In the end, this mechatronics approach encouraged a team-wide engineering solution. It also led to more accurate and timely predictions of the system's reaction, which helped meet customer goals for the new kiosk.
|
About the Author(s)
You May Also Like