Truck gages get on the bus
October 7, 1996
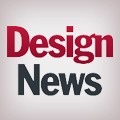
Grand Junction, CO--At first glance, it looks deceptively simple: A dashboard gage, small enough to fit in a child's palm. It's housed in a plain black-and-white plastic enclosure, a couple of strands of twisted-pair wire dangling from its back.
For truckbuilders, that "simple" gage holds a wealth of potential. The wiring it eliminates behind the typical truck dashboard could fill a basketball. The inventory part numbers it purges are even more impressive. Instead of stocking up to 42 different kinds of two-inch gages, truckbuilders now need to keep only one. The reason: The new SmartGage, as it is called, can be anything it wants: an air-pressure or axle-temperature gage, or a gage for measuring volts, amps, oil pressure, fuel pressure, manifold pressure, oil temperature, fuel filter vacuum or any of 33 other functions. Up to now, all of those functions were served by dedicated gages that truckbuilders kept on their shelves.
The advantages of SmartGage, however, don't end with reduction in wiring and inventory. The device solves a multitude of problems for assemblers, users, and maintenance personnel. It vastly simplifies the wiring process, eliminates the need to replace burned out incandescent bulbs, moves oil and air hoses away from the dashboard, and diagnoses its own problems.
How could one little gage do so much? The answer is contained in two simple words: data bus. Using available data buses, engineers tapped into a mountain of information that previously lay dormant.
The story of how they accomplished that, however, is not so simple. Engineers involved in the project struggled with the concepts and implementation. They spent hundreds of hours in test labs and criss-crossed countless miles between development sites in Texas, Colorado, and Washington. "Between track time and the test bench, we did over a million miles of testing," recalls Tony Briski, Peterbilt engineer and co-inventor of the system.
Partnership a key. Briski conjured up the idea for the SmartGage in 1992 after noticing a curious phenomenon in truck dashboard design. There were about 260 circuits in most vehicles, he found, comprising about 1,000 feet of wire. Much of it was discrete wiring leading from engine sensors to individual gages on the dashboard. If a customer wanted to monitor engine oil pressure, for example, assemblers screwed a pressure sensor in the side of the engine block and ran wires from it to the dashboard gage. They did the same for water pressure, coolant temperature, and other gages.
Yet, Briski knew that about half of Peterbilt's engines were electronically controlled in 1992. That meant that much of the data was already gathered at a single point in the engine. He wondered if he could tap into that data bank with a single set of wires and eliminate much of the complexity. Peterbilt's chief engineer, Bob Morrison, encouraged Briski to model his idea and enter into an inventor's contest sponsored by Peterbilt's parent company, PACCAR Inc.
"I'd had enough experience in cab electrical to immediately see the logic in what Tony was proposing," Morrison recalls. "It was viable, given the fact that we were moving to electronic engines."
Briski took up Morrison's offer and pursued it with the kind of aggressive determination that only an inventor could muster. He formulated an idea for an addressable gage--one that could tap into the available data bus, "listen" to all of the information zipping through the lines, pick out the data that was right for it, and display it. To accomplish that, Briski considered a variety of techniques: optical; mechanical, capacitive; Hall Effect; and others. Then, he travelled the country to visit gage makers.
Briski's travels ultimately brought him to the desert-like town of Grand Junction, CO, where he visited AMETEK/Dixson. There, he spoke with engineers who saw the value in his concept and suggested a solution. To minimize manufacturing costs, they recommended a mechanical addressing technique. The solution: a punch-card method that works like the Hollerith cards used in the early days of computing (see sidebar).
"We discussed other methods," recalls Dennis Coleman, vice president of engineering for AMETEK/Dixson and co-holder of the now-patented addressable gage concept. "But the other ideas didn't make sense from a manufacturability or cost point of view."
To facilitate development of the concept, Peterbilt struck a deal with AMETEK/Dixson: Peterbilt would buy the SmartGages from them, share joint patent rights, and enter into a royalty agreement. In return, AMETEK/Dixson would apply their engineering expertise in a partnership aimed at development of the new SmartGage.
Award-winning idea. With the basic concept for the SmartGage in hand, Briski returned to Peterbilt's engineering facility in Newark, CA, and went to work. He drew up a rough sketch for the PACCAR Inventor's Award contest and wrote a short prospectus. Then he cobbled together a crude prototype using plastic PVC pipe, telephone wire, and telephone jacks. "I made some very convincing gages, including wires, needles, and glass," he recalls. "They looked like real gages."
Indeed, Briski's prototypes looked real enough to win him the PACCAR Inventor's Award early in 1993. With the confidence that corporate recognition brings, he then travelled to Denton, TX, to discuss the gage's features with workers in Peterbilt's electrical assembly area. He attended several weekly meetings where assemblers talked about manufacturing problems and schedules.
Next, he introduced the concept of the SmartGage to the assembly workers and asked for their input. They agreed that eliminating handfuls of wiring was a good idea, then suggested features to further simplify assembly. Among them: a simple twist-lock technique for easier gage installation, and a way to keep pressurized fluids and pneumatic hoses farther from the dashboard. "Most of the design features were suggested by people in the assembly area," Briski says. "My idea was to do telephone-type wiring and a scale plate. The rest was their's."
At the same time, Briski and Peterbilt engineers continued to work with engineers at AMETEK/Dixson. In Grand Junction, the hard task of developing a manufacturable product had just begun. They still needed to perfect the addressable scale plate and design an enclosure that employed a simple twist-lock. They also needed to develop an effective sealing technology for the gage, put together a manufacturable printed-circuit board, and conjure up a technique to move the hydraulic and pneumatic hoses away from the dashboard. "The basic idea was simple," Briski says. "The details were enormous."
Groundbreaking design. At AMETEK/Dixson, staff members set to work on designing a product. Engineers laid out the mechanical design on CAD, using Parametric Technologies' Pro/ENGINEER software. Their goal was to replace the traditional metal enclosure with a plastic composite version. Using a special twist-lock mechanism, they wanted to simplify gage installation and eliminate assembly difficulties. On CAD, they developed a plastic composite enclosure, a surrounding plastic composite clamp ring, and a snap-on bezel that would eliminate the crimping of metal that took place on conventional gages.
AMETEK/Dixson's biggest challenge, however, was to develop a "brain box" to eliminate the need for pressurized fluids and pneumatic lines in the cab. In most big truck cabs, drivers want gages that provide information not available through the engine's ECU. That includes oil pressures, fuel levels, axle temperatures, air-brake pressures, and a host of other data. Conventional trucks provide this information by running pressurized fluids and pneumatic lines to the back of the dashboard. For assemblers, those lines add to the already complex task of wiring the gages. The additional lines also create the possibility of fluid spillage in the cab.
AMETEK/Dixson engineers proposed to eliminate those problems by developing the brain box, or chassis interface module, and connecting it via data bus to the dashboard. Their interface module consisted of a metal enclosure topped by five sensor plates designed for connection to air, oil, fuel, and vacuum sensors. A printed-circuit board located inside the enclosure would gather information and convert it for use on the data bus. Because the module would be located in a hostile, outdoor environment, engineers potted the PC board in poly-urethane, employed waterproof connectors, and designed it to resist radio frequency and electromagnetic interference.
In the meantime, AMETEK/Dixson's mechanical engineering team continued work on the gage's enclosure. They built stereolithography (SLA) models of all the mechanical gage parts, including the housing, clamp ring, and bezel. Afterwards, they called the staff together to witness a clamp-ring test. "With SLA models, you shouldn't conduct tests more than a few times," explains Mike Cox, SmartGage's project manager. "The parts are very brittle. So we called a meeting, brought all of our engineers into a conference room, then watched a one-time test of the snap fit." The test proved successful; the gasket on the model showed sufficient compression, and AMETEK/Dixson adopted the configuration.
As the design progressed, Briski also worked with staff members at PACCAR's Technical Center in Mt. Vernon, WA. There, an ergonomicist teamed with Briski on the development of the display. She changed the LED from green to amber for easier reading. She implored test subjects to read the display in full sun, indirect light, twilight, and night light. Technicians installed the unit on a truck, then logged more than 10,000 miles on a test track.
All the while, Briski travelled back and forth to the Technical Center, logging more than 20 trips to Washington during a six-month period. Engineers there devised tests to prepare the interface module for use in the worst possible environment: a garbage truck. They tested it for placement in high moisture, dust, temperature, salt spray, and corrosive chemicals. Finally, after moving to the Peterbilt office in Denton, TX, a tech center engineer sent Briski a technical verdict via e-mail: "SmartGage lives."
More than a wiring saver. In July 1994, Peterbilt introduced SmartGage to the truck-buying public at the International Trucking Show in Anaheim. "We knew from the response at the show that SmartGage would be well received," notes Morrison. "Customers looked at the display and then returned with their friends to show them how it worked."
After the show, Peterbilt took the final steps to introduce SmartGage on a production vehicle. A team of engineers further developed the concept as a production-feasible design. They built discrete wiring harnesses to run from the interface module to the cab, then designed smaller jumper harnesses for the twisted-pair wire behind the dashboard.
In the first quarter of 1995, Peterbilt introduced the Smart Gage on its Model 320 truck, often used as a refuse hauler. The company quickly found that it was well-suited to the application.
Briski says that on trucks employing 20 or more gages, SmartGage can eliminate a cubic foot of wiring from the dashboard, amounting to about 10 lbs. One data cable, replaces, on average, about 116 wires. The ability to reduce complexity in big vehicles gives the SmartGage possibilities in cranes, buses, mining, equipment, and agricultural vehicles, as well as on-road trucks.
Assemblers and customers found that the device had other advantages. The simplicity of the twist-lock mechanism diminished the potential for repetitive hand injuries by reducing the shock force on assemblers' wrists. Self-diagnostics simplified troubleshooting, and LEDs eliminated the problem of burned out incandescent bulbs in the dashboard.
"The original idea was to simplify the wiring," Coleman concludes. "But in the final implementation, it turned out to be much more than that."
Timeline for design
JUNE 1992-- SmartGage concept conceived
AUGUST 1992-- AMETEK/Dixson selected as development partner
MAY 1993-- AMETEK/Dixson begins electrical design
OCTOBER 1993-- Prototype installed at PACCAR Technical Center
APRIL 1994-- Test, break, fix, retest
JULY 1994-- Introduction at International Trucking Show
JANUARY 1995-- Introduction of Smart Gage on Peterbilt Model 320 truck
What Am I? SmartGage Knows
THE PATENTED CONCEPT in the Smart Gage centers on a punch-card-type addressable scale-plate technique. This addressing methodology enables the gage to "know" what it is--a fuel-level or oil-pressure gage, for example.
Although engineers at Peterbilt and AMETEK/Dixson considered other techniques, they settled on the "punch card" because it was easily manufacturable. Using the punch-card method, each gage employs a polycarbonate scale plate with identifying decals. An integral polycarbonate tail stretches from the scale plate to the bottom of the gage. There, it slips in between a set of five beryllium-copper fingers and contact pads.
The key to the concept is a set of small holes in the polycarbonate tail that corresponds to each of the beryllium-copper fingers. If a finger has a corresponding Mylar(R) hole, then it can touch the contact pad and current is allowed to flow. If no hole is present, the finger cannot touch the pad, therefore current does not flow. In this way, each finger becomes a part of the particular gage's address. If only the first and last of the five fingers are allowed to touch the contact pad, for example, then the gage has a binary address of 01110.
By "knowing" its binary address, the electronics in each gage can "listen" for messages on the data bus that apply to it. As a result, each gage hears all of the data in the stream, then picks off the messages intended for it alone. All other data are ignored.
After SmartGage "hears" its address, it operates like any conventional gage. Several of the bytes of information it receives are regarded as "pointer position data." Those bytes pass through the data bus to a microprocessor. The microprocessor uses that data to energize coils that move the pointer to the proper position above the scale plate.
The key to the concept is the scale plate, says Tony Briski, co-inventor of the technique. "Without the scale plate, the gage doesn't know what it is," Briski explains. "But when you plug in the scale plate, it suddenly knows."
About the Author(s)
You May Also Like