Intelligent dishwasher outsmarts dirt
April 10, 1995
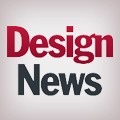
Newton, IA-- Anyone who's done the dishes knows that you clean until the dish is done and not a moment longer. Most dishwashers, on the other hand, do just the opposite-they over-clean. To accommodate heavy loads and dried-on, stubborn foods, the typical dishwasher runs longer than necessary-wasting water, electricity, and time.
Not so with the IntelliSense(TM) dishwasher. To improve on the traditional "blind" dishwasher design, an engineering team from Maytag and Honeywell's Micro Switch Division spent the past two years designing a dishwasher with a mind of its own. Aided by sensors and fuzzy logic, their dishwasher uses closed-loop feedback to fine-tune its operation. Among other smart moves, when sensor output indicates that the wash water is clean, the dishwasher stops washing.
The result? IntelliSense carries a DOE rating of $44 annual energy use-21% better than the current DOE standard. The washer also uses 6.5 gallons of water per load, vs. an average 9 gallons for other U.S. makes, and 5.8 gallons for European brands, claims Maytag.
The "smarts" of the IntelliSense reside in a collection of sophisticated sensors linked to a central microprocessor. When combined with fuzzy-logic control, these technologies allow the dishwasher to behave like an "intelligent" appliance. It selectively uses data to make performance decisions.
Like sensors used in cars, the main sensor assembly in the IntelliSense provides feedback about essential, ever-changing operating conditions such as the amount of detergent and food soil in the water. To do this, the dishwasher uses a photoelectric turbidity sensor, a conductivity sensor, a temperature sensor, and a position sensor to determine the wash arm's R.P.M.
Sensor headquarters. Getting to market quickly was a top priority for Micro Switch and Maytag engineers. Perhaps the most difficult decision for the team was where to locate the sensor assembly. Finally opting for easiest manufacturability, they chose a small space inside the water pump. The choice created new challenges, especially with the visible-light-based turbidity sensor. The sensor uses an LED transmitter and receivers for both transmitted and reflected light to provide feedback about the amount of food particles circulating in the water.
Senior Maytag design engineer Douglas Gardner explains: "Turbidity sensors in general are flow-through devices, but every place we looked was either expensive in terms of manufacturing, or had bubbles-and bubbles look like food." In addition to making the washer more manufacturable, putting the sensor in the pump provides adequate current to determine water conditions-without requiring the typical flow that would generate deceptive air bubbles.
"To complicate things, many powder detergents look like food soil, and liquid detergents look like water to the turbidity sensor," says Senior Maytag Design Engineer Mitch Corbett. To the engineers' dismay, in-house testing revealed big differences between generic and name-brand detergent chemistries; Some soap manufacturers also changed formulas during Maytag's test period.
To get around the detergent problem, engineers chose a conductivity sensor. "By providing feedback about wash-water chemistry, it allows us to know if we're seeing food soil and detergent or just food soil," explains Corbett.
Guided by Micro Switch engineers, the team designed an on-board microprocessor to signal-condition sensor output. This "smart sensor" capability allows the sensors to communicate directly with the fuzzy-logic control.
Before the sensor group finalized the technologies they would combine for accurate sensing, another team began designing the assembly's snap-fit enclosure. Inside the pump, nearly constant exposure to hot water and a highly alkaline solution that includes chlorine and bleaches practically begs for trouble. "We needed strength of snaps, scratch resistance, clarity, and environmental resistance," says Maytag Senior Design Engineer Randy Cooper. They also needed a twenty-year seal to last the expected life of the product.
Again working closely with Micro Switch, Cooper and his colleagues created a "plastic sandwich" of two snap-fits compressing an O-ring to encapsulate the assembly. FEA and Parametric Technology's Pro/ENGINEER software allowed engineers to design the enclosure body and very thin snaps to fit the small pump cavity. Engineers chose Udel(TM) polysulfone resin from Amoco Performance Products because it maintains its clarity and withstands high temperatures without crazing, clouding, or cracking, says Cooper.
No time to spare. Misleading bubbles and a hostile operating environment aside, the Micro Switch/Maytag design team had no easy task in assigning functions to the sensor values. Deciding which data painted the most accurate picture of washing conditions proved difficult-and an aggressive schedule added to the challenge.
As one group juggled sensor components and signal ratios, other engineers began writing the algorithms that would translate sensor output into function. "We were shooting at a moving target for the first nine months as we were trying to develop the algorithms," recalls Corbett. "We went through four or five iterations of sensors."
After some agonizing, engineers chose a 6805 microprocessor chip from Motorola, Austin, TX, as the main microprocessor. Availability and tools were top concerns. "We wanted to get a C compiler that we could use to do high-level language design with this product," says Corbett. The 6805 gave them a suite of tools, a price within budget, and the I/O requirements and peripheral support they wanted, he adds.
A critical time-saver was a fuzzy-logic development software package called Fide from Aptronix, Santa Clara, CA. The Windows-based package allows users to set up fuzzy logic sets and rules, then compiles the code down to assembly language. This software allowed Maytag engineers to put the language directly into the microprocessor to call as functions in the IntelliSense's code. "We needed both the fuzzy-logic tool and the high-level language so we could develop this product as quickly and painlessly as possible," adds Corbett.
Unable to wait for a completed controller, engineers used PCs to run early prototype dishwashers. Fide compiles both to assembly code for the microprocessor and can compile to C programs for a PC. This capability allowed the group to do all-important early simulations.
For example, engineers took data from a dirty cycle and tested how dirty the dishwasher "thought" the dishes were. "We could take those data points and plug them into Fide, and it would tell us exactly what the fuzzy logic rules and sets were giving us as an output," says Corbett. "I could manipulate the rules and sets that way; It was a lot easier." Engineers programmed the IntelliSense to track the previous 36 washings to establish user habits and anticipate washing demand.
Backlit display. When it came to designing the control panel display, engineers were torn between two requirements: To provide a lot of options for a high-end machine, and to be as simple and straightforward as possible.
The final design uses a backlit display for simplicity and for its ability to present additional options on command. When the options are not backlit, the user has only three choices: more options, start, or delay.
Choosing a light source wasn't easy. "We evaluated electroluminescent, light piping through fiber-optic mats, LED backlighting, LCDs, touchscreens-and we came back to incandescent," says Gardner. "It's a very low-cost technique to implement, and it's straightforward."
Incandescent lighting is usually taboo on appliances, where thermal cycles and vibration wreak havoc on delicate filaments. "Micro Switch applies the same technology for Apache helicopter instrument panels, and we figured the reliability required for that application might suit our needs," laughs Gardner.
To prevent lamp burn-out, engineers wired the lamps to be energized slightly for a short period of time. That warms up the filament and limits the end-rush current before the lamp turns on completely, reducing filament stress significantly, says Gardner. When the user hits a button, there's a 30- to 50-millisecond delay that the human eye cannot recognize. The lamp is wired to experience the same filament warming while the dishwasher door is open. Keeping the filament warm in this manner prevents an aged filament from being brittle.
To satisfy lamp reliability requirements, engineers did door-slam tests of more than half-a-million cycles. "We tested to the point of breaking hinges off the doors-and we're quite satisfied with the reliability," says Gardner. Micro Switch also provided shock and vibration and resonant-frequency analysis tests.
Shared parts. Manufacturability was an issue at every design session. Says Cooper: "The challenge was to not change the basic structure. We wanted a fuzzy-knowledge, adaptively controlled machine without making drastic tooling changes." In the final analysis, shared-parts engineering yielded a smart dishwasher that in many ways looks just like its conventional cousins.
With an eye to the future, engineers made the IntelliSense "total-home" or "smart house" capable: It could be controlled by a central controller. And some day, it may share a network with a smart refrigerator, clothes dryer, or vacuum cleaner. Although no new projects have been announced, the Maytag/Micro Switch team feel that the IntelliSense effort achieved a hands-down success. Would they do it again in the name of another smart appliance? Says Gardner: "There were a lot of headaches and variables you don't have control over. But there's nothing boring about development engineering. You don't twiddle your thumbs."
A co-destiny relationship
In terms of engineering organization, the IntelliSense design project was radically different from anything Maytag had attempted in the past. "It was a co-destiny partnership," explains Curran Cotton, vice president of research and development at Maytag. "Honeywell knows sensors, and we know appliances."
"Bringing in Honeywell at ground zero to design these parts involved a lot of trust," says Maytag's Gardner. "We didn't work with another team; they were part of the team. And allowing somebody else to be that closely involved is really scary because the work is a competitive secret."
It turned out to be a good risk. Micro Switch design engineers and other fuzzy-logic experts came to work on-site with Maytag for more than three months. Many other Honeywell engineers were involved throughout the design. "Working with them really helped us take a "big picture' look at everything," adds Maytag's Cooper.
Keeping everybody on the same page presented a challenge at times. Engineers used the Internet and videoconferences, and Honeywell allowed Maytag team-members to log into their main computer system. "Trust was essential," says Honeywell Business Development Manager Paul Ludwig.
That trust paid off in speed to market, says Cotton. Industry Analyst Gerry Beatty of Home Furnishings Network agrees. "Maytag was very anxious to get this product to market as quickly as possible, because competitors are headed in same general direction."
Beatty predicts that computer chips and sensors will soon be in many major appliances. "Maytag took it one step further with fuzzy logic. They applied existing technology in a new way-something more designers will consider."
As white-goods manufacturers trim product development cycles and add new features, consumers can expect to see product changes that were "unseen just a few years ago," adds Beatty.
Meet the Alpha User
Georgia Barnett of Saratoga, CA, will go down in Maytag history as the first Intelli-Sense owner.
Market research has shown that few consumers consider energy savings as a deciding factor in their choice of home appliances. To Barnett, a top consideration was noise. Thanks to an additional 14 lbs of insulation, "It's so quiet," she says. "The dishwasher I'd had before was loud."
Barnett says she was also impressed by the timer that indicates remaining cycle time, and the option of a heat-less dry cycle to reduce energy costs. "The dishes aren't hot or wet when it's finished," she adds. "And I know it uses less water."
About the Author(s)
You May Also Like