European standards shine spotlight on EMI
September 25, 1995
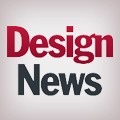
A man opens his car hood and falls into a coma. Cause and effect? Yes. It's an extreme example of electromagnetic interference, or EMI.
The man was diabetic and had a computer-controlled insulin-injection system. Insulin demand is a function of activity rate, and the computer monitored the man's pulse rate and respiration and pumped out insulin accordingly. When he opened the car hood, an electromagnetic field from keying the ignition system interfered with the injection system's electronics. The result: three days' worth of insulin in 60 seconds.
The manufacturer (who shall remain nameless) took the medical device to Instrument Specialties' World Compliance Center (WCC) in Delaware Water Gap, PA. The Center tested it for susceptibility to external emissions. The end result was that the firm took the product off the market because there was no way to guarantee that under every possible circumstance such a tragedy wouldn't happen again.
EMI has become more and more of a problem as electronic products proliferate. Simply stated, EMI causes a piece of electrical equipment to misbehave due to unwanted electrical energy in the wrong place at the wrong time. (RFI, or radio-frequency interference, is a subset of EMI.)
Most people don't get bent out of shape when a hair dryer interferes with their TV picture. But, as in the above example, many EMI problems are not so benign. In the U.S., all airplanes ban the use of cellular phones because of possible interference with avionics equipment, and 50% of all hospitals ban cell phones. In fact, in a recent episode of the TV series ER, a cellular phone caused a wheelchair to spin around and an electromagnetic problem with a woman's pacemaker caused her arm to jerk up and down.
European standards. In the U.S., the FCC has set standards so that the emissions from certain electronics equipment don't interfere with allocated radio spectrum channels. The European Community has gone further by setting standards for both emissions and susceptibility to emissions for all electronic equipment.
"That's because the countries are so close," explains Instrument Specialties' Product Manager Art Johnson. "They wanted to control emissions more closely so you wouldn't have Germany doing one thing and Belgium doing something else, which could result in bad interference problems. In the U.S., we have one communications system, so there's no chance of anything happening between New York and Connecticut." But it should concern U.S. design engineers.
If you want to ship any electronic product to Europe after midnight December 31, 1995, your product must comply with the EC's electromagnetic compatibility (EMC) standards. If it doesn't, you'll be committing a criminal offense and be subject to fines and imprisonment. However, the main deterrent to not complying is the cost of losing access to the European marketplace--even for a short time.
Five U.S. industries--automotive, medical, industrial control, telecommunications, and test and measurement equipment--never had to meet any U.S. FCC requirements. But now they have to meet the more stringent EC regulations to ship to Europe. "It's been a real shocker for them," says Ron Brewer, vice president of EMC technical services at Instrument Specialties (IS).
Many testing facilities, such as Instrument Specialties' World Compliance Center, have been certified by an European Competent Body to test electronic systems to the European Community's EMC Directive. IS also manufactures standard and custom shielding products to help solve EMI problems.
It's most cost-effective to contact such a facility early so that you can avoid EMI problems. But human nature being what it is, many companies wait until a design is nearly finished and on the production line before addressing EMC. Some discover they have a major problem that requires a total redesign of their equipment. Others can get by with adding shielding or gasketing or doing some other simple retrofit.
Few passing grades. "About 90% of all products we test for EMC fail the first time," says Brewer. For example, a leading international maker of handheld cellular phones had Instrument Specialties' WCC test a model that had already passed FCC tests for compliance with the European EMC standards. They fully expected it to pass, thinking that the plastic housing's plated-nickel conductive coating provided sufficient grounding and shielding for the pc boards. They were wrong.
"The phone failed the emission portion of the testing," says Tony Sosnowski, manager of product development. "We designed a custom shield that not only acted as a barrier between the two circuit boards, but also grounded the top and bottom covers." The shield, made from beryllium copper 25 alloy, has 90o flanges that provide the contact between the covers. Using this first prototype shield, the phone passed the European tests. Within a week, Instrument Specialties was tooled up and making the custom part.
A surgical laser already used in the U.S. for trimming drooping eyelids and other delicate types of surgery was recently tested by the WCC. The power the laser puts out determines the depth of cut. EMI susceptibility testing for the EC EMC standard showed that the depth of cut could vary by almost .75 inch. "Instead of trimming your eyelid," says Brewer, "it could bore a hole through your skull and into the front part of your brain."
Instrument Specialties is working with the manufacturer on a major redesign. The two decided that just adding more shielding, which protects a device from EMI, wouldn't be the best solution. The shielding could degrade, and the manufacturer wanted a fail-safe design. Possible design changes include adding a power-regulator circuit, filtering circuits, and perhaps more shielding.
A European maker of telephone switching equipment approached Instrument Specialties during the early design phase to address EMC. The application: a cable access carrier. The company wanted end-users to have enough cable openings, but not have to worry about EMI problems if a cable slot wasn't being used.
Instrument Specialties engineers designed a nickel-graphite, conductive-elastomer shield that slides into unused cable access slots. "If there were nothing in the slot, RF energy could seep through the hole," explains Instrument Specialties' Art Johnson. Under pressure, the silicone-polymer-based elastomer makes contact with both sides of the metal carrier, prohibiting energy from passing through. If the part were metal, you'd need very fine tolerances to ensure electrical contact.
Testing for compliance. The World Compliance Center has a variety of rooms for performing different EMC tests. For instance, to find out the kind of radiation levels a piece of equipment is emitting, and not be confused by the ambient environment, WCC makes some preliminary measurements inside a shielded room, or enclosure. These enclosures exclude exterior RF ambient.
A typical measurement can have error due to antenna loading, reflections off the inside walls, and resonance that occurs when the wavelengths of frequencies happen to coincide with the dimensions of the enclosure. To minimize that problem, the floor, ceiling, and walls are covered with anechoic material. This material, in the form of bright blue cones, contains ferrite and carbon particles that match the impedance of free space. If a radio wave propagates along, what little reflection there is reflects into the cones and not back into the room.
"They're kind of wild places," says Ron Brewer, vice president of EMC technical services, of these rooms. "When the door is closed and the lights off, the sound-absorbing qualities of this material will let you hear your heart beat."
The Center also does susceptibility measurements in the shielded enclosures to prevent pollution of the environment. "The FCC and FAA take a dim view of squirting RF out into the ambient," notes Brewer.
A room without metal. If a product passes the shielded-enclosure tests, it proceeds straight to the top of the WCC. "We have a special area upstairs--our 10m open-area test site," says Brewer. The European EMC Directive states that radiated emission measurements must be performed in an environment where there are no reflections. Therefore, this room has no metal--not even nails--above the ground plane.
Fiberglass bolts hold the walls together, and the windows have plastic frames. Lights and wiring are below floor level, with the light shining up through the shield. As far as radio waves are concerned, the room is outside.
During emissions testing, engineers set up a calibrated receiver with calibrated antennas. They measure the field intensity generated by the sample at a distance determined by the appropriate standard. A camera watches the sample on the turntable as it rotates 360 degrees, and the antenna moves up and down to gather a wide spectrum of data. This is the test most products fail.
Even if a product passes, that doesn't mean life will be rosy. "Passing EMC testing in the lab doesn't necessarily mean that the unit will operate properly in the field," stresses Brewer. A lab can't possibly duplicate all real-world conditions. Good design still applies.
EMC resources
Two helpful guides to the EC electromagnetic compatibility standards are The Guide to the EMC Directive 89/336/EEC and EDN's Designer's Guide to Electromagnetic Compatibility. The first describes the key features of the European Directive, their implications, and how to form a plan to achieve compliance. The second addresses design engineers who need to get up to speed on EMI, why it happens, and how to fix it.
The Guide to the EMC Directive 89/336/EEC, by Chris Marshman, IEEE Press, Piscataway, NJ, 1993 (ISBN 0-7803-0445-4).
EDN's Designer's Guide to Electromagnetic Compatibility, by Daryl Gerke and Bill Kimmel. To order, phone (800) 523-9654 or FAX (708) 390-2779.
About the Author(s)
You May Also Like