Engineering News 7438
December 16, 1996
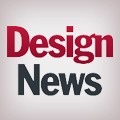
Newton, MA--As companies face increased pressure to design for assembly, manufacturability, and serviceability, designing out fasteners is becoming more common. In industries such as computers and telecommunications, that means turning to snap-fit parts.
"Snap-fit fastening eliminates extra parts, and is essentially free," says Lee Winick, mechanical lead engineer for desktop products at Sun Microsystems, Mountain View, CA. "Any cost-sensitive or commodity industry will consider them. Since the computer industry is rapidly moving to the commodity end of the spectrum, snap fits are becoming more attractive there."
A prime example: Sun's Ultra 1 Workstation. The unit's front grill, which attaches to the top cover, is held in place with seven small plastic snaps. The rear-power-supply cosmetic bezel hooks into place on one end and snaps in at the other. The motherboard card guides snap in place on the bottom of the chassis, as well.
In addition, the front fan, used to cool the drives, and the system speaker snap into a plastic bracket in the front of the workstation. The bracket itself then snaps into the unit's metal base.
The LED lightpipe holds the LED and cable, and snaps into the front wall of the chassis. The LED sits in front of the lightpipe and snaps into the top cover. A purple bezel around the CD and floppy opening also snaps into place on the chassis.
Expanding use. With the introduction of its 02 workstation (See "'02' takes over for Indy on the desktop", Design News, October 21, 1996, page 41), Mountain View, CA-based Silicon Graphics Inc. (SGI) is also embracing snap-fit technology.
What prompted SGI's move to snap-fit parts? Decreasing the number of fasteners in a product reduces costs, says John Barco, product manager at the company. Manufacturability was also key. "It's easier to build systems that are modular and snap together, and it takes less manufacturing time," he says. Another big consideration: user serviceability. "Now the end user can service the system in his/her location without requiring specialized tools," Barco explains.
Designed mainly in Pro/ENGINEER software (Parametric Technology Corp., Waltham, MA) running on SGI systems, the 02 is unlike traditional box-style units that sit under the monitor, or "towers" that rest on the floor. Instead, the 02 workstation stands to the side of the monitor.
A closer look. The sheet-metal chassis, which provides the EMI and safety enclosures and houses all the system boards and modules, consists of six different metal parts. Each of these features a tab-and-slot design, enabling all six parts to interlock like a puzzle. Four rivets hold everything together. The final assembly uses integral rivets. Placed in multiple locations, these rivets bring structural rigidity to the chassis. More importantly, they provide needed EMI shielding.
Within the chassis, the AV module has a complete snap-together design that comprises two clamshell plastic parts. The board is snapped into one half, and the top cover snapped onto it, creating a completely enclosed module. And, though it does have screws for EMI shielding, the system-board also snaps into the carrier.
In the unit's base plastic, or skirt, a speaker is inserted into a plastic bracket that is snapped into the skirt. A button array, a plastic part with four separate buttons molded into it on cantilevers, doglegs into one side of the skirt, and snaps in place again. The unit's lightpipe, which brings two LEDs to the exterior as a single lightpipe, also snaps in place.
The main chassis, comprising those six interlocked parts, drops into the skirt, and is slid sideways about 1/4 inch. Four integral snaps molded into the skirt hold the chassis in place.
More ease, less time. Each of the 02's modules, including the power supply, hard drive, and system-board module, features an injection-molded, Delrin, rotating-cam mechanism. This mechanism inserts and extracts the particular module into the sheet-metal chassis. A thread-forming screw holds each mechanism into its module. "We had a design that allowed the mechanisms to snap into place, but were concerned about its ability to resist the shear forces involved in driving the modules into their mating connectors," says Bob Riccomini, product design department manager.
The goal was to make all the modules customer serviceable. "Many of our customers are savvy enough to take apart their systems, and wanted to do it on their own," says Ujesh Desai, Products & Technologies public relations associate at SGI. "We feel they should be able to do that," adds Barco.
Perhaps most important is the potential time savings should a module fail. Explains Riccomini, "A technician can troubleshoot the problem from our support line and ship a new module to the customer. S/he can swap the parts him/herself and be back on-line in less than 24 hours."
With the new system in place, virtually all of the 02's main components are customer serviceable. The user simply pulls down with moderate pressure on a plastic lever that unlocks the mechanism, allowing the selected internal device to slide out.
"Designing this system was more complex than a traditional box design, but the benefits greatly outweigh the costs," says Barco.
Sun and SGI aren't the only companies heading away from fasteners and toward snap-fit parts. According to Jack Murphy, director of the Structural Plastics Division of the Society of the Plastics Industry, Washington, D.C., snap-fit technology is becoming an increasingly bright option for many companies in the telecommunications and business equipment industries.
"And, with the improving relationship between OEMs and molders, use of snap fits is likely to occur more often," he says.
But does this move toward snap-fit parts signal the impending demise of the fastener industry? Not likely, says Charlie Wilson, director of engineering at the Industrial Fasteners Institute, Cleveland, OH.
"In the long haul, we won't see huge designing-out issues. We may see fewer fasteners being used, but that doesn't necessarily mean a more sophisticated fastener isn't replacing a number that have been taken out."
Leon Attarian, manager of marketing information and communication at Penn Engineering & Manufacturing Corp., Danboro, PA, agrees. "Many companies are switching to a snap-on type of hardware that lets them reduce parts count by one piece," he says. "But they are still using actual hardware.
"More people will consider switching to snap fits because everyone is looking for ways to reduce costs and number of parts," he adds, "but the applications seem limited to consumer industries with a focus on high volume and less service."
Certainly, Attarian admits, plastics have made some new applications easier. "But, with the dramatic growth of product applications," he counters, "the metal fasteners industry isn't losing anything."
--Deana Colucci, Associate Editor
Gas-assist and resin team for tough amplifier housing
Arlington Heights, IL--Advanced design and protoyping, gas-assist technology, and three engineering resins merged to help Motorola's linear power amplifiers leap the next-generation canyon. The result: a lighter, stronger, smaller, more cost-effective, and more aesthetically pleasing cellular infrastructure than cast-aluminum predecessors.
The amplifier's assembly consists of a housing made of 10% glass-filled Makrolon(R) 9415 polycarbonate, two covers of Bayblend(R) FR 110 polycarbonate/ABS blend, and, because the product will be used extensively in earthquake-prone environments, two seismic retention latches made of Makrolon 6485 polycarbonate--all supplied by Bayer Corp.'s Polymers Div., Pittsburgh. The housing and covers use a gas-assist technology in their production, while the latches are straight injection molded.
The very thin, flat covers could not have been achieved with traditional injection molding, according to Joyce Sprau, mechanical staff designer at the Motorola Cellular Infrastructure Group. Gas-assist also let Motorola design a hollow handle that is more aesthetically pleasing and has a better ergonomic feel when carried by the installation technician.
The amplifier's assembly, which measures 91.67 x 12.83 x 4.20 inches, has a wall thickness of only 0.157 inch and uses 4.8 lbs of plastic. Because of Motorola's goal of reduced product development cycles, the company used rapid prototyping to help optimize gate sizes, locations, and gas channels, eliminating major changes and costs in the final tool.
"The right prototype choices were essential to prove the strength and robustness of a design before production molds were started," Sprau explains. "Bayer helped tremendously by providing mold flow and structural analyses." The three protoyping phases included: selective laser sintering, silicone-rubber-mold rapid tooling, and spray-metal-mold rapid tooling.
While running the first housing parts, changes were easily made to the spray-metal tool to optimize gate and gas channel sizes. Once a good part was made, changes were incorporated into the CAD model for the production tool. All thermal, structural, drop, and seismic testing was also completed before the production tool was started.
Sajar Plastics Inc., Middlefield, OH, uses Nitrojection(R) gas-assist technology from Nitrojection Corp., Chagrin Falls, OH, to mold the housing and top and bottom covers. With this process, the mold is filled 80% to 85% and the nitrogen gas injected in two stages through the nozzle at pressures under 2,000 lbs. The gas channels in the cover have a square rather than star pattern because of component height restrictions inside the module.
Following demolding, two latches are attached to the housing. The covers are then affixed with only three screws by taking advantage of "hinging" features along one side of the cover. The latches connect the finished assembly to a cage during installation. No other assembly or finishing is required, improving recyclability and lowering cost.
Composites produce light, efficient city bus
El Segundo, CA--Through the use of composites, engineers at Northrop Grumman have created a prototype 21st-century city transit bus that weighs 21,800 lbs--9,000 lbs less than a similar bus made from metal. Consisting of just four major assemblies (versus the usual 250), the hull design of the 72-passenger Advanced Technology Transit Bus (ATTB) dramatically reduces assembly time and part count, while eliminating corrosion problems, slashing fuel costs by roughly 20%, and extending useful life to 25 years.
It's constructed entirely from E Glass in a matrix of Dow Chemical Company's (Midland, MI) Derakane(R) epoxy vinyl ester resin. The flat areas of the walls, floor, and ceiling consist of 2-inch-thick panels with a closed-cell PVC foam core, while complex areas use dry glass preforms. The preforms and fabric layers are vacuum bagged and infused with resin in a proprietary vacuum-assisted resin-transfer molding process (VARTM).
The primary structure consists of a lower tub (a single piece 37.5 ft long, 8.5 ft wide, and 3.5 ft deep), a ceiling, and two window belts. The four are bonded together entirely without fasteners. Exceptionally robust, the hull has withstood a simulated side impact from a 4000-lb car at 25 mph, sustaining no damage that would require repair.
Dow formulated a special grade of Derakane 441-400 resin for VARTM. Engineers also chose the resin because it doesn't creep and cures at room temperature.
On a per-pound basis, composites typically cost more than steel. But Dave DeMent, manager of integrated product definition at Northrop Grumman, believes that the ATTB hull can be built for roughly the same price as a metal one. "You're trading off a large number of steel parts and their assembly for a more expensive material, but less assembly time," he says.
Innovation isn't limited to the composite hull. The bus features a hybrid propulsion system in which a compressed natural gas (CNG) engine drives an electric generator that powers two electric motors, one at each rear wheel. Future plans include a flywheel that may be used to store recovered braking energy.
Engineers also designed a unique wheelchair lift to address what is currently the biggest maintenance item on city buses. The ATTB sits low to ground, and instead of a lift it uses a ramp that extends with a linear actuator.
Six prototypes are scheduled to be built by the end of 1997. Should all go well, Northrop Grumman plans to transfer the technology to a bus manufacturer.
--Mark A. Gottschalk, Western Technical Editor
The Hannover Fair helps U.S. companies target international market
Newton, MA--Gone are the days when companies could rely solely on their own turf to turn a profit. The problem: Though the European Union's single-market economy represents more than 345 million consumers and $6 trillion of purchasing power, cracking the EU can be difficult for "outsiders."
That's why companies from around the globe attend the Hannover Fair in Hannover, Germany. The fair, celebrating its 50th anniversary in 1997, covers nine sectors ranging from factory equipment and automation to power transmission technology. This year alone some 7,000 exhibitors from more than 60 countries will be showcasing their services and products.
Nearly 90% of the 330,000 attendees at the fair make procurement decisions in their companies. Twenty percent of those visitors come from outside the European Union. Special exhibits and sessions will be held for companies seeking new overseas opportunities.
One example: The International Business Forum will bring together potential partners interested in global trade and new markets, as well as in cooperation and new contacts. Institutions and organizations from all parts of Europe, Latin America, and Pacific Asia will offer essential information and decision-making assistance.
Visitors to the the Hannover Fair come from all business sectors. Exhibitors can thus forge direct links with decision-makers from industry, as well as the services sector and the public sector. And forge they do.
Tim Dehne, vice president of marketing at National Instruments, offers his experience at the '96 fair. "Because the show was so big, we had numerous occasions to work on business opportunities with other exhibitors, and we made significant inroads with new customers.
"We were also able to introduce those new customers to how they could better apply the computer to their automotive needs and thus be more productive," explains Dehne, who plans on returning to the fair in '97.
To best utilize their time at the fair, U.S. companies can exhibit in the USA Pavilion, which provides direct access to an international cross-section of qualified industry professionals.
The Pavilion will include sections for American manufacturers of power transmission, hydraulics, pneumatics, and motion control; industrial automation; rail-transport technology; and subcontracting and industrial materials. Other exhibit options for American manufacturers include the USA Lighting Technology Pavilion, the Power Transmission Distributors Association Pavilion, and the National Fluid Power Association (NFPA) Pavilion.
To date, the NFPA has 19 exhibitors lined up for its pavilion. Director of Expositions Bill Prueser is not surprised at the fair's popularity. "It is an excellent place to introduce your product to the European market," he explains. "In 1993 one of our members lined up six agreements with new distributors."
There are other advantages as well. "In the European tradition, people tend not to accept cold calls from a salesperson, making introduction very difficult, if not impossible. But once you meet a person on the show floor, they are willing to set up an appointment. The Fair really facilitates future meetings," Prueser says.
"Throughout its history, the Hannover Fair has highlighted an unparalleled cross-section of the newest and the best the world's industrial manufacturers have to offer," says Andrea Anderson, USA Project Director for the Hannover Fair. "With the strong participation we expect for the USA Pavilion, we will do the same for American-made products and technologies. It is our aim to heighten international awareness of U.S. industry."
Smart sensors improve aluminum production
Mosjoen, Norway--Needing to increase the productivity, yield, and quality of its casting operation, Elkem Aluminum A/S selected self-contained, high-speed industrial sensors from Selcom AB in Partille, Sweden.
The SLS-5000 sensor samples data at 16 kHz and has a built-in processor for data averaging and filtering. It works by projecting a fixed beam of light to the surface to be measured. When the light hits the surface, it scatters. The sensor collects part of the scattered light, focuses the image of the light spot onto its position detector, and uses optical triangulation to determine distance.
To regulate the level of molten aluminum in the launder, Elkem installed three SLS-5000 laser sensors on each of its two tilting furnaces 7.8 inches above the distribution trough. This distance was twice that of the other sensors Elkem was evaluating, which let the company better control the amount of aluminum flowing to the molds. Level data from the sensors determined the mass remaining in each furnace within plus or minus 1,100 lbs.
Engineers used a third sensor to control furnace tilt as aluminum flowed from the furnace down a channel to the casting table. Controlling tilt ensured a consistent pour and flow rate of the molten aluminum to the molds. Tilt was controlled to within plus or minus 0.04 inch by sending sensor data to a PLC for real-time feedback.
This sensor let Elkem monitor the variation of casting lengths to within 1.17%--almost 5 times greater than the company originally specified.
Elkem also uses the sensors to control the aluminum level in molds. The rate of flow is a function of metal height and throttling of a stopper rod actuator, which is controlled through the PLC. As the level in the mold decreases, the system automatically increases the flow rate to ensure uniformity for casting accuracy and consistency.
"By accurately and consistently controlling the flow and the level of aluminum in the mold, we can now better control surface quality and yield, and decrease scrap." says Elkem engineer Inge Jan Thorvaldsen.
Shaking out cabin noise
Cary, NC--It takes a flight in a puddle jumper to remind the business traveler grown soft on Boeing and Airbus just how noisy planes can be.
Insulation works best on high-frequency sound, and much of the offending vibrations in aircraft are of the low-frequency variety. Therefore, designers at Lord Corp. elected to attack the problem directly by making some waves of their own.
The Lord NVX Active Control System employs sensors, actuators, and amplifiers in custom configurations under the direction of a controller to reduce in-flight cabin noise by as much as 80 percent. Rebecca Weih, engineer and NVX program manager of Lord's Fixed Wing Business Unit, says the equipment can be applied to a variety of turboprop and turbofan aircraft, either as refits or as OEM installations.
Basically, the NVX systems cancel noise by producing vibrations. These are done with actuators mounted on the engine pylons or in the airframe or from speakers inside the cabin. The actuators produce structural vibrations that counteract undesired vibrations from the aircraft's engines, while the speakers cancel noise with "anti-noise." The arrangement of actuators and/or speakers is custom-fitted for each aircraft type. Lord engineers used Matlab analysis software to model noise levels.
The key to Lord's NVX systems is a controller developed with the cooperation of Lockheed Martin. The unit receives engine, sensor, and cabin microphone input, and coordinates all actuator and speaker output. The controller adjusts sound-canceling devices throughout the flight according to real-time input. All NVX installations use the same controller, although the algorithms they are programmed with vary according to the physics of the application.
Most of the bothersome noise from turboprops comes from prop wash. Vibrations are transmitted through the air between the propellers and the airframe and on into the cabin. Microphones inside the cabin sample noise levels. The controller activates the sound suppression agents: actuators under the trim of larger planes and speakers under the seats of smaller ones.
Aircraft with fuselage-mounted turbofans, such as the Cessna Citation and McDonnell Douglas DC-9/MD-80, transmit vibrations through the pylons to the cabin. Accelerometers in the engine add to the input from cabin microphones. The actuators are positioned on the pylons where the engines connect with the fuselage.
Weih says NVX's actuators do not produce any additional stress on the airframe and even reduce it by canceling stress-producing vibrations. Cessna is installing NVX on new Citation X private jets, and Beech Aircraft has approved the equipment as an authorized refit for its King-Air turboprops.
Intergraph unveils 4-Pentium-Pro workstation
Huntsville, AL--Intergraph has unveiled what's believed to be the first "personal-workstation-class" computer featuring four Pentium Pro processors. The TD-610 is likely to prompt software companies to develop versions of their programs that can take advantage of all four processors to solve one compute-intensive problem.
Already, during the Autofact trade show in Detroit, ANSYS announced a multi-thread version of its analysis software for the Intergraph four-processor machine. And for other applications not tuned to use four processors at once, the TD-610 offers power enough so engineers can run a complex analysis problem in "background" while continuing to do design work using other software.
"They understand how to make systems that 'gang' multiple processors," says Bruce Jenkins with the Daratech consulting firm. "They're consistently pushing the envelope in getting performance."
The TD-610 was part of a wide-ranging product an-nouncement that also included Intergraph's lowest-priced workstation entries. The least expensive model, a Pentium TD-20, sells for $1,495; the Pentium Pro version TD-200 starts at $2,595. Intergraph's Intense add-in 3-D graphics card brings the TD-200 to $4,995. The four-processor TD-610 starts at $13,500.
The TD-610 as well as the 310 (single Pentium Pro) and 410 (dual processors) come with up to 1G RAM, Ultra SCSI disk subsystem with data transfer up to 20MB/sec, an Ethernet controller that can automatically take advantage of 100-Mbit/sec data rates when available, and 8X CD-ROM drive.
Touchpad technology cuts power use
Camarillo, CA--Interlink Electronics has developed semiconductive touchpad technology company officials say uses 85% less power than conventional capacitive techniques.
A VersaPad module built around the technology is aimed at battery-operated devices such as notebook PCs, cordless keyboards, and remote controls. Unlike capacitive pads, which constantly monitor for finger positions, the VersaPad can drop into "sleep mode" until activated by stylus or touch. During a recent demonstration, the pad consumed less than 1 microamp at rest, while a capacitive touchpad used more than 2 milliamps.
"It may save 10 to 15 minutes on portable-PC battery life," says Interlink spokesman Keith Roberts, in an industry where battery longevity is a major selling point. Interlink's Force Sensing Resistor can be used with a stylus or gloved hand, something capacitive pads cannot accommodate, he added.
Alpha PC software speeds Windows
Maynard, MA--Digital FX!32 software from Digital Equipment Corp. uses translation--not emulation--technology so DEC Alpha-based systems can run 32-bit Windows applications as fast or faster than they run on comparable Intel x86 systems.
Using emulation to get non-x86 CPUs to run Windows applications results in performance loss. "With Digital FX!32, Windows applications run 5 to 20 times faster than they run under emulation," claims Ed Caldwell, vice president of Digital Semiconductor, a DEC business. DEC has evolved this translation technology over several years by developing three generations of binary translators: VAX to Alpha migration, MIPS and SPARC to Alpha, and now x86 to Alpha.
Third-party CPU benchmarks have shown that an Alpha 21164 500-MHz system running a test version of Digital FX!32 was on par with a 200-MHz Pentium Pro system. In typical applications such as Microsoft Word and Excel for Windows95, National Software Testing Laboratories tests indicate that Alpha performance under Digital FX!32 is comparable with Pentium Pro systems running at 150 to 200 MHz.
"Digital FX!32 translation technology runs x86 NT code at speeds approaching that of the fastest Intel processors," says Martin Reynolds of Dataquest, a San Jose-based market-research firm. "With native Alpha NT Office just around the corner, Digital FX!32 for other major applications, and emulation for legacy applications, Alpha can do a good job with the broad Windows and DOS code base."
Current Alpha users can get Digital FX!32 software free by downloading it from DEC's WWW site: http://www.service.digital.com/FX32.
Slip into this awards contest
Wilmington, DE--Need an extra $5,000? Then consider entering the 1997 DuPont Plunkett Awards for Innovation with Teflon(R).
The program, conducted worldwide, encompasses regional awards from the Americas, Europe, and Asia Pacific. The awards focus on the most innovative commercial products marketed during the last five years that incorporate Teflon and Tefzel(R) fluoropolymer resins, films, fibers, finishes, or DuPont fluoropolymer products licensed under the Teflon trademark. The deadline for entries from the Americas is January 24, 1997.
Winners are selected from a wide range of applications: aerospace, automotive, environmental, telecommunications, chemical process, electronics, and wire and cable, among others. The first-place winner in each region receives a specially designed crystal sculpture and $5,000. Second and third prize winners will receive $3,000, and $1,500, respectively, as well as a commemorative plaque. All winners will be recognized at regional award events in the early spring of 1997.
The award generates considerable recognition throughout the industry. The 1995 winner, John Spencer of W.L. Gore & Associates, testifies: "It's very satisfying to be recognized by DuPont. At Gore, everyone knows what it means to get a Plunkett Award, so we get great internal recognition for this as well."
Gore won its award for "GLIDE" dental floss. Because of its natural slipperiness, the addition of Teflon to the floss not only makes flossing easier but more comfortable, since the soft edges of the floss help prevent gum irritation. Two years after its introduction, Glide became the second leading brand of dental floss sold at retail in the U.S.
To obtain Plunkett Awards entry forms, phone (800) 432-7436 or visit http://www.dupont.com/corp/whats-new/releases/950921.asp on the Internet.
Carbon graphite adds new twist to pretzel making
Hanover, PA--Inside a traveling oven that bakes pretzels, the average temperature during the 24-hour, seven-day-a-week process averages 270F, while the bearings revolve at about 3 rpm. The high heat makes it impossible to provide lubrication.
That's what faced the bearings at the Wege Pretzel factory. But thanks to their self-lubricating, carbon-graphite construction, they stand up to the task.
In the past, Wege produced its pretzels in a round oven that featured a stone floor and circular, turning hearth. After their insertion onto the hearth, the pretzels were removed following a certain number of revolutions. However, the ovens required several people to operate because of the need to insert and remove the product.
Enter new traveling ovens with wire mesh belts that run through them. A gear motor located outside the oven powers the belts through a series of large friction rollers that run through the oven. The advantage: automated transfer of the pretzels onto the belts, making it possible for one person to operate the oven.
Bearing life proved critical in the design of the ovens. The bearings, supplied by the Dodge Div. of Reliance Electric/Rockwell International, Greenville, SC, are pressed into the ends of the rollers that travel through the oven. Reliance found that the self-lubricating carbon-graphite, produced by the Pure Carbon Co., St. Marys, PA, can withstand the oven's extreme heat. When the bearing rubs against metal or ceramics, a microscopically thin graphite film is quickly laid down on the shaft, helping to control temperature rise during operation.
Carbon-graphite can hold up under even more extreme conditions, reports Reliance Electric's Maury D'Hoore. General-service carbons can weather temperatures up to 600F, special grades up to 1,000F.
Dodge Dakota takes instrument panel to new level
Detroit--The automotive instrument panel (IP) took a big step forward with the introduction of the 1997 Dodge Dakota. In fact, futurists say the design may ultimately lead to complete modularization of vehicle interiors.
The fully integrated structural IP went from a blank sheet of paper to production in 30 months. The modular component is used on the full range of Dakota models, from 3,600 to 5,900 lbs gross vehicle weight. It meets all performance requirements--without the need to make any manufacturing or assembly changes.
Chrysler spearheaded the design as part of its Extended Enterprise concept, which began in late 1993. This includes engineers from Chrysler's vehicle platform engineering and manufacturing groups, Textron Automotive Co., and Dow Automotive.
"In keeping with the concept, there was open dialogue among the participants from the very beginning," says Stan Surratt, manager of resident engineering at Chrysler's Sterling Heights Assembly Plant. Surratt served as manager of interior systems for the program, and was a key participant in the development of the structural IP.
"We were aware that Dow had done pioneering work in structural IPs," Surratt explains. "They had been doing design modeling and FEA correlation studies with engineering thermoplastics for a number of years. That made them a logical choice to work on the program."
Textron Automotive supplied the instrument panel for the previous Dakota truck. It also was involved in advanced IP development and manufacturing. Its selection as the Tier I supplier came early in the development process.
Dow's role was to support a total system design that included: concept, performance criteria, material selection, engineering analysis and performance, and manufacturing optimization. "Simply explained, we were to furnish design and engineering analysis to help achieve Chrysler's objectives," says Jim Kolb, Dow's business director for Chrysler.
These objectives reflect the concerns that OEMs face in addressing what Chrysler describes as "the voice of the customer:"
- Occupant safety performance that complies with FMVSS 208 requirements.
- Improved climate control, including 30% better defroster performance, and doubled demister flow.
- Better overall fit and finish than conventional IPs.
- Minimized buzz/squeak/rattle--a major warranty concern.
- NVH of at least 30 Hz for a smoother, quieter ride.
The multi-functional design's center provides the primary structure for the IP. All components are referenced to this part, which encompasses the driver side, lower center, close-out panel, and the passenger-side glove-box surround. The passenger-side airbag mounts directly to the panel without the need for steel reinforcement.
The front panel mounts to the body-in-white and forms the backbone of the structure. It is the first part forward in the vehicle, and consists of a door-to-door sweep of the climate-control ducting with various molded-in features. When the front and center panels are joined, they form a two-piece, air-tight monocoque construction that has a structure and stiffness greater than conventional steel IPs.
Fresh air for the windshield defrost is delivered through a network of manifolds and outlets formed by the assembled moldings. The cross section provides smooth, continuous distribution of structural stiffness along the duct, while maintaining airflow delivery, air velocity, and all the needed packaging requirements.
The rear panel adds structure when it is vibration-welded to the center panel assembly. It also mounts the cluster, climate-control head, radio, demister adapt-er, air-flow distribution deflectors, and trim plate.
The glove-box assembly, molded with Dow's Pulse(R) ABS/PC alloy, went from a three- to two-piece design, saving the cost of an entire tool. The box's bin and ribbed inner structure are molded in a single piece that includes a one-time living hinge. The assembly also has molded-in hinges for attachment to the IP assembly, further minimizing assembly steps and cutting costs.
Steel crush plates and roll-up end brackets assist in directing the load to the upper structural duct that distributes the load to the body-in-white. An upper pad and trim panels made with the Pulse resin complete the structural assembly.
The design of the Dakota IP reduces part count by more than 50% from a traditional design, while saving weight and cost. In addition, the system improves performance and incorporates a passenger-side airbag not previously required.
Lightweight bus bars help power space station
Rolling Meadows, IL--The Space Station "Freedom" is equipped with four solar arrays, each of which provide 23 kW of power to run both the station's internal systems and on-board experiments. To function, the arrays will depend on lightweight bus bars for power distribution.
The sophisticated bus-bar power-distribution system was designed by engineers at Rockwell International's Rocketdyne Div. and the Network Buss Div. of Methode Electronics Inc., Rolling Meadows, IL. "It was a unanimous aggreement that a multi-layer laminated bus-bar assembly was necessary to achieve the design goals," explains Denis Lindsey, engineering manager at Methode. "The qualification testing of pre-flight models has verified the success of the design."
The primary function of the system is distributing filtered dc power, utilizing multiple, laminated bus-bar assemblies. The bus bars are positioned near the solar arrays in shielded modules. There are 62 sizes; the largest bar measures 10 x 7 x 4 inches, the smallest 3 x 3/4 x 1 inches.
"There are numerous mechanical, electrical, and safety features incorporated into the design of the laminated assembly," says Lindsey. These include a one-piece laminated construction containing five discrete conductors for accurate installation; permanent, integral terminal markings located on accurately positioned low-insertion-force connectors; and efficient, low-inductance, power distribution in a lightweight pluggable assembly, with the assembly geometry readily adapted to the space allocated.
The requirements for materials launched into space differ greatly from those on earth. Temperature, weight, and environmental differences all had to be considered when designing the system. "The selective lamination and final mechanical assembly of the pluggable connector hardware required several iterations to develop a model that, through testing, meets the design expectations," explains Lindsey.
DuPont's Kapton(R), Teflon(R), Tefzel(R), and silicone were chosen as insulators because of their ability to withstand the wide temperature ranges of space. Electrical optimization, increased flexibility, and weight reduction are accomplished by reducing copper cross-sections in selected areas. The engineers are machining the copper, resulting in heavier power-distribution sections and thinner connection.
Rocketdyne, in conjunction with NASA, is testing the system using a series of engineering and qualification modules before releasing the component for actual flight.
About the Author(s)
You May Also Like