Top Pain Points in Optomechatronic System Design
Successful optomechatronic designs depend upon collaboration among optical, mechanical, and electrical engineers as well as these other factors.
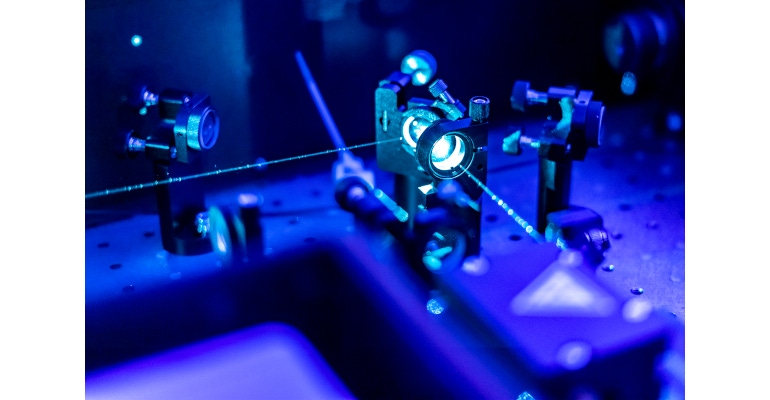
Optomechatronic systems bring unique challenges to product design. While simple optical elements, like light pipes, can be fairly straightforward to create without much in-depth knowledge of optics, systems involving the use of light sources and receiving circuitry require unique skills from a diverse team. As the name implies, optomechatronic system design generally requires the participation of optical, mechanical, and electrical engineers.
Many companies have a basic understanding of optics but lack organic optical engineering resources and underestimate the value that is brought by a dedicated optical engineer. A qualified optical engineer will bring both a deep understanding of the physics involved and expertise in the manufacturing capabilities necessary for the product volumes and performance specifications. In many complex systems, it is impossible to get a result that meets the performance requirements without a collaborative team with diverse skills.
Following are a few of the unique pain points for successful optomechatronic systems design.
Imaging System Issues
Aberrations (i.e., deviations from ideal imaging behavior) can lead to image distortion, reduced resolution, and degraded image quality. Correcting for aberrations requires careful optical design, selection of appropriate optical components, and advanced corrective techniques.
Diffraction and scattering are frequent issues. Light waves diffract and scatter as they interact with optical and mechanical components, leading to reduced contrast, image degradation, and loss of information. Managing diffraction and scattering effects is crucial in optical system design, especially in high-resolution imaging systems or systems that require high dynamic range.
Scarce Optical Engineering Talent
While one can find consultants in academia or with a pure science focus, finding optical engineering expertise with a mindset toward production is challenging. The education and experience in physics is unique and is not often combined with the skills of an engineer. You may not always need an optical engineer but, when you do, you will need one badly. A consulting firm with optical expertise in its portfolio may be one way around the shortage of talent.
Clear and Practical Customer Expectations for Optomechatronic Designs
As with most development projects, it is critically important to have a good handle on the performance requirements for an optical system. Creating specifications that are too tight may result in constraints that are not manufacturable at the right cost for the volumes needed. In some cases, over-constraint on the specification can result in product requirements that cannot be satisfied in high-volume manufacture or at a price that fits within the product budget.
Likewise, optical systems involving a variety of opto-mechanical and opto-electronic components can be time consuming to create. Oftentimes, it is crucial to have a mathematical model that includes electrical and mechanical tolerances. This can take a surprising amount of time to do properly. Without such analysis, a development team can embark on a path that is simply not producible with high yield or at a reasonable cost.
Budget & Scheduling That Accommodate Risk
Optical systems need to have schedule and development budgets that adequately support the optical analysis involving a multidisciplinary team. One cannot depend solely on paper analysis to validate a design approach. The team needs to create prototypes to prove the theoretical capabilities of the design. Components are expensive in small quantities, and there are very long lead times for custom parts (6 months or more). Custom lenses can cost $50K or more in prototype quantities.
Tolerance Analysis
In any design, especially where high precision or manufacturability are a concern, tolerance analysis is an important step in ensuring repeatability in the face of component and module performance variability. In the case of mechanical or electrical designs, it may be sufficient to simply consider the tolerances within the respective mechanical or electrical subsystem. However, when designing an optomechatronic system, it is usually necessary to consider the tolerance build up in mechanical, electrical, and optical components. Such analysis requires a solid understanding of statistical tolerance control and manufacturing capabilities. The analysis is complex and requires collaboration and input from all three disciplines.
Furthermore, the results of the analysis need prototype construction and testing to validate results. All this is time consuming and requires talent with deep understanding, so these steps should be part of any project plan. If the team does not have these skills internally, it may be a good idea to seek out a consulting firm with such capabilities to assist. Mistakes made through incorrect tolerance analysis can result in excessive schedule delays and expense.
Fixed vs. Adjusted System Designs
When performance targets are rigorous or manufacturing and component tolerances create too much variability in the finished product, it may be necessary to design adjustability into the system. This is not an ideal situation for many products as introducing optomechanical adjustability into a design represents an expensive step in the manufacturing process and the potential for added maintenance requirements. Only through a thorough tolerance analysis can it be determined whether a design is robust enough to hit the operational goals without the need for adjustments.
Unique Tools and Testing Required
Optomechatronic design depends on unique tools that require specialized know-how to operate properly. Such tools can be expensive to acquire (or buy on a subscription basis). Likewise, prototyping and testing often require access to an optical bench along with specialized tools and test equipment. These test setups are not common and can be expensive to provision in a lab.
Of all the product designs systems, optomechatronic systems represent the pinnacle of complexity. Proper design requires a combination of unique talent and equipment, both of which are scarce (and expensive). The process requires accommodation for special risks and therefore mandates the need for thorough design analysis and testing to validate analytical results.
About the Author(s)
You May Also Like