Solid Edge ST4 Melds Direct, Feature-Based Modeling
June 30, 2011
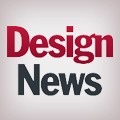
The marriage of direct modeling and history-based modeling continues to evolve with the latest CAD releases, and Siemens PLM Software's recent launch of Solid Edge ST4 is no exception.
Building on the foundation laid in Solid Edge ST3, Siemens PLM Software took further steps to enable machine designers and engineers to work within a history-based or direct modeling paradigm depending on what's best-suited for the task within the same product.
For example, starting with Solid Edge ST3, users were able to tap synchronous features for doing fast and flexible edits to models while, at the same time, adding ordered features for the design of process-type parts. This latest release adds additional feature types and modeling capabilities within the synchronous workflow, essentially letting engineers do what they traditionally did within an ordered workflow within the more flexible direct modeling environment.
Bridging the two modeling paradigms has been a focal point for most of the major CAD vendors, not just Siemens PLM Software. In its recent release of Creo, PTC's next-generation CAD platform, the firm introduced a direct modeling and parametric modeling capability as part of a family of integrated Any Role Apps. This is an evolution of its original strategy where the Pro/Engineer history-based tool was a completely separate and unrelated offering from the CoCreate direct modeling package.
Without presenting a complete laundry list of new features and functions, here are a couple of new commands and capabilities lumped under the Synchronous Technology umbrella that were highlighted by Kris Kaspzak, director of Solid Edge marketing at Siemens PLM Software, in a recent interview:
New 3D modeling relationships and commands to help facilitate the centering, offsetting, and editing of native or imported geometry.
A new automated "live sections" capability to more quickly create and edit revolved parts like shafts; the live sections transfer dimensions defined in 2D to the editable Live Section on the 3D model.
Features for improving assembly relationships -- for example, one new capability that simplifies centering parts, maintaining the centered location when adjacent parts are edited, moved, or animated.
A new Web Network synchronous command for creating ribs and webs used in plastic parts that need stiffening. Each time users want to modify the rib structure, they simply drag the face of the web, and only the affected 3D geometry regenerates.
Beyond the new Synchronous Technology enhancements, there are new features for facilitating the use of multi-CAD and to boost collaboration, including the ability to leverage JT data (Siemens PLM Software's lightweight 3D data format that is widely used across industry) in assemblies. There is also a new feature that lets parts and assemblies be directly saved to the 3D PDF format for viewing and sharing using Adobe Reader software.
About the Author(s)
You May Also Like