Contacts ensure precision, reliability
December 3, 2001
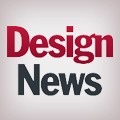
Electrical contacts fabricated from stamped metal are fairly simple, right? After forming, they are traditionally "tumble" polished with abrasives to remove burrs left after stamping.
But as sensors using such contacts become more demanding in their applications, such as automotive throttle control today and by-wire systems in the future, the often uneven and inconsistent results achieved with tumble polishing are less acceptable. Problems include subtle differences in contact shape between individual contacts, leading to variations in performances.
|
In the case of a position sensor, the metal contact often slides over a screen-printed resistive track on softer conductive plastic. Lack of precision in deburring can leave irregularities that generate excessive wear, cutting contact life and changing electrical characteristics, such as resolution.
Safety in critical automotive systems calls for design lifetimes on the order of 100 million cycles. That's something conventionally made contacts cannot consistently deliver, according to Michael Tucci, president of Micro Contacts Inc. He cites throttle control as an example, where the pedal position is electrically determined and drives the throttle body setting without any mechanical linkage. Such systems are found on most cars and trucks.
For such crucial applications, Micro Contacts has developed a proprietary contact fabrication and polishing method that not only produces consistent part-to-part results with better polishing, but also allows flexibility in contact tip shapes. "It's a mechanical erosion process that grinds a uniform supply of strip held in such a manner as to achieve uniformity," says Tucci. "There's no overly sexy technology," with the method being like the action of a file removing burrs on the contact tip in a continuous strip. The "inline process" grinds each part to the same finish, whether it is a radius or a flat chisel point.
The technique allows engineers flexibility in designing products with respect to geometry and materials, adds Tucci. "We can design tip geometry to customer specs and not have them design to our process." The polishing method is useable across a wide range of material composition, hardness, and heat treatment.
One customer is Frank Dietrich, U.K.-based managing director for AB Electronic Ltd., a fabricator of potentiometers used in many industries. For the automotive industry, AB Electronic makes potentiometer sensors for throttle-pedal position, headlight leveling, active suspension, and exhaust gas recirculation systems. "The contact wiper is very important, being 50% of reliability," Dietrich says. "With Micro Contacts polishing, angle or linear position is very accurate-0.01% or better-while conventional contacts have ten times worse repeatability."
Dietrich says that only about 2% in cost would be saved without using the Micro Contacts process, which gives a long contact life even under 175C temperatures in an engine compartment. Tucci notes that, "if you have a low-resolution, robust system that can handle a non-filed part," you may not want the slight added cost of the polishing process.
Additional Details |
Contact Diane Vespoli, Micro Contacts Inc., 62 Alpha Plaza, Hicksville, NY 11801-2695; Tel: (516) 433-4830; Fax: (516) 433-6379; E-mail: [email protected] ; or Enter 502 |
About the Author(s)
You May Also Like