Taking the Risk Out of Robots
Small manufacturers are taking a big chance when they invest in robotics. Yet there are strategies to reduce that risk.
January 24, 2024
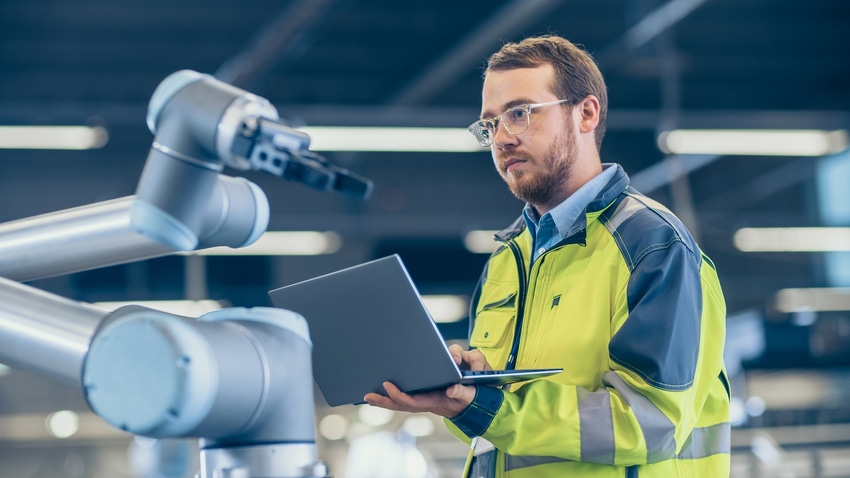
At a Glance
- Robot risks
- Workforce issues
- Robot expertise
A resilient national manufacturing industry needs manufacturers of all sizes that are empowered to operate at peak efficiency. This is particularly true for small and medium sized manufacturers. There are nearly 600,000 small manufacturers in the US. They constitute 99% of all manufacturing enterprises.
However, small- and medium-sized manufacturers are more likely to struggle with workforce shortages. They operate on smaller margins, and they have fewer resources to adopt advanced manufacturing technology.
Smaller firms typically have a negligible R&D budget. They have less time for development, and they may not have the internal team needed to adequately evaluate and research solutions. In short, these firms could benefit from the use of robotics but often lack the resources needed to de-risk and adopt robotics.
Jay Douglass, COO at ARM Institute will dig into this subject in his presentation, De-Risking Robotics for Manufacturing, at IME West on Tuesday, February 6 at 1:00 pm.
Helping Reduce Robot Risk
The ARM Institute has created the Robotics Manufacturing Hub, a no-cost service funded through the Southwestern Pennsylvania Build Back Better Regional Challenge Award. The goal is to help manufacturers – particularly small operations – navigate and minimize the risks associated with adopting robotics. ARM helps companies explore off-the-shelf solutions and solve unique technical challenges through prototyping at the Pittsburgh facility. This presentation at IME West will explore the de-risking process for robotics in manufacturing, offer lessons learned, and show the impact being spurred by the ARM Institute through its Robotics Manufacturing Hub.
We caught up with Jay Douglass to get some background on the ARM Institute and the issues small manufacturers face when they adopt robotics.
Could you tell us about the ARM Institute?
Jay Douglass: We are a public/private organization partly funded by US Defense Department. The ARM Institute is a consortium of 450 companies. We publish problem statements and invite our members to form teams and send in proposals to create answers to these problem statements. Most of the issues involve robots and manufacturing. So our members tend to be manufacturers and robotics companies.
What are the barriers now for small manufacturers adopting robots?
Jay Douglass: The key thing is expertise. Small manufacturers don’t have robotic technicians or engineers. It’s a daunting exercise to deploy robots without that expertise. In many cases, the small manufacturers are under pressure because of the need to remain competitive. They’re also facing workforce issues. The aging workforce is retiring, so skills are getting lost. In some cases, they’re turning to robots to compensate.
Robot costs are coming down. Are they coming down enough for small manufacturers?
Jay Douglass: Yes, but the bigger problem is they don’t have the skillset. They don’t have the knowledge to make the right decisions and to operate the equipment. Robots are becoming more functional, and the cost is dropping. That’s helpful. Plus, AI is making new things possible with robots. Thanks to AI, they’re easier to operate.
Are robots becoming more flexible? Can they be redeployed for different tasks?
Jay Douglass: Robots are more functional. They can be used in a variety of environments. In the past it was for one thing like welding or painting. Now robots and be repurposed and they can be moved around more easily.
Are manufacturers adopting robots to stay competitive?
Jay Douglass: Eighty five percent or all robots are at car companies. But that’s changing every year. Not robots do more than spot welding or painting. Line workers are using robots to do the dull, dirty, and dangerous jobs that people don’t like. If you’re working on an electric grinder all day long, you’re happy to turn that over to a robot. It’s better for everybody. Robots don’t get hurt and they can work 24/7. They’re productive all the time, not just during the workday. Robots make the workplace a better environment for the manufacturing industry.
About the Author(s)
You May Also Like