Tomorrow’s 3DP Technology Is a Reality at Our Universities
Protolabs is working with college programs to push 3D printing technology into space, racing, and the deep blue sea.
January 26, 2023
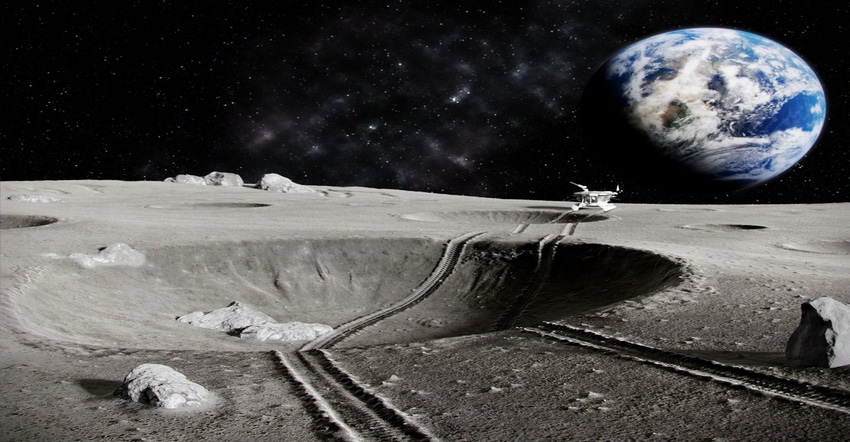
Mike Kenison, VP of the Americas, Protolabs
A career in digital manufacturing has offered me a front-row seat to the innovation that revolutionizes industries. From the rise of electric vehicles to life-saving medical devices, our industry plays a vital role in bringing products to market faster so they can benefit our everyday lives. From this unique perspective, I can confidently say I have never been more excited about the future of innovation in our country.
But following a year of continued supply chain disruption, global unrest, and economic turbulence, what is the source of my optimism? In short, it is the tremendous work being done on college campuses.
Protolabs partnered with universities across the country over the last year to help students design, build and create ideas that push the limits of what one may think is possible for a team of undergraduates. We had the opportunity to experience their technical expertise and incredible enthusiasm firsthand.
For a company that works with leading Fortune 500 innovators, that answer may surprise you so I would like to share a few examples of the projects that have left me inspired.
Space Enterprise Berkeley Shoots for the Moon
The 40 University of California-Berkeley students who make up Space Enterprise Berkeley (SEB) come from a wide variety of educational backgrounds all with the same goal: Not only launch the first-ever liquid-fueled rocket at UC-Berkeley but do so spectacularly, surpassing the Karman Line nearly 330,000 feet above sea level.
Eureka-1 was the result of three years of hard work, 14 successful fire tests, and 24 stressful hours in the Mojave Desert. Protolabs worked with the SEB team to 3D print the rocket’s plenum and parachute components via Selective Laser Sintering using PA12 40% Glass-filled, which is a stiff material that offers long-term wear resistance.
The team was able to 3D print organic geometries including lattice patterns to lightweight the part while retaining a similar strength-to-weight ratio.
“Designing with lattices and utilizing additive manufacturing allows you to have this very flexible design space that you can parameterize and quickly edit and change according to your constraints,” explained SEB’s Low Altitude Demonstrator Program Lead Asa Garner. “We have a significant section of the bulkhead, essentially the volume in the part that is the lattice space. According to variables that we can change, we can move in our simulation where the pressure comes from, where we’re putting in the bolts, and have that lattice automatically regenerate.”
The result was SEB becoming one of only 10 colleges in the country to successfully launch a liquid bipropellant rocket and achieve the fourth-highest altitude within that group. While short of their Karman Line goal, the team was thrilled with the result.
“When Space Enterprise at Berkeley was founded, nobody could have foreseen the immense challenges of building a liquid bipropellant rocket. Yet, three years later, after thousands of hours of work by hundreds of members, old and new, we have finally achieved this first step towards space,” the team said in a post-launch statement.
Fueling Formula-Style Racing
Formula One racing had a meteoric rise in popularity with American fans last year, but the sport has long been a borderline obsession for the thousands of students comprising Formula SAE teams nationwide. The competition, organized by the Society of Automotive Engineers, provides the perfect arena for future engineers and product developers to implement their technical skills for the sake of speed.
Protolabs worked with undergrad students in teams at UC-Berkeley, Northwestern, the University of Illinois Urbana – Champaign, and the University of Michigan-Dearborn, lending manufacturing grants to fund 3D-printed and CNC-machined parts for their innovative electric- and combustion-powered vehicles.
Quick-turn iteration was the name of the game for each team as they raced to develop, build and test their vehicle before competitions last summer, and Protolabs was excited to be along for the ride. CNC-machined accumulator mounts, suspension rockers, wheel adapter assemblies, and more were delivered in 48 hours as teams burned the midnight oil. 3D printing for its design freedom and light-weighting abilities also played a vital role.
The Northwestern Formula team 3D printed six sets of battery cell holders in glass-filled nylon using SLS. The rigid material was chosen to withstand not only the lateral accelerations of the car but also the large loads applied to the cell holders when the cells are ultrasonically welded to each other. SLS combined with the durability of nylon allowed for the necessary design freedom.
The Formula EV team at UC-Berkeley turned to 3D printing at Protolabs for their car’s high-voltage box, which houses the battery and the different components responsible for the efficient transfer of energy. The box required an intricate design that integrated the different mounting structures directly into the inner casing of the box, removing additional spacers and fasteners typically required in the overall system. The part also needed to be made of a material that was heat resistant while offering insulation to prevent energy loss—PA 11 offered both without sacrificing tensile strength. The simplified design of the part was a success, with the team now planning to 3D print all their enclosures in the future.
Deep Sea Exploration with MIT’s DOUG
Two-thirds of the earth’s surface is ocean, and we currently monitor less than 2 percent of it. Only about 5 percent of the world’s ocean has ever been explored. Massachusetts Institute of Technology (MIT) students set out to change that with their Deep Ocean Underwater Glider, affectionately named DOUG.
Equipped with a suite of navigation and communication tools, DOUG was designed to reach depths of 1,000 meters. The beauty of DOUG lies in its energy source: The student team designed it for long-endurance missions by storing energy-dense hydrogen in the form of aluminum fuel. The aluminum fuel is stored onboard and is reacted with water at depth to create hydrogen. The reaction expels water from the vehicle, acting as a buoyancy engine that brings the vehicle to the surface. At the surface, the hydrogen is fed into a fuel cell to generate electricity and charge a battery pack to power the next dive.
The team worked with Protolabs to 3D print custom cell spacers using Multi Jet Fusion technology in PA 12 Black and machined tube couplers in aluminum. Both would play a vital role in the overall buoyancy of DOUG.
As an autonomous underwater vehicle, the applications for DOUG are significant. For one, DOUG’s endurance could be used to monitor the more than 26,000 miles of undersea pipelines in the Gulf of Mexico. Currently monitored with less-than-reliable sensors and divers, a school of DOUGs would provide early warnings of catastrophic leaks from underwater pipelines.
Investing in a Brighter Future
The next generation of engineers and product developers are using their time as students to take on the challenges of today and tomorrow. Our leading institutions are providing not only the necessary technical expertise but also a platform to develop skills honed outside of the classroom.
Whether it is building a rocket, Formula car, or UAV, students leading each project are developing the dedication and drive that will be vital in their careers. We are proud to foster their growth as an investment in the future of innovation.
You May Also Like